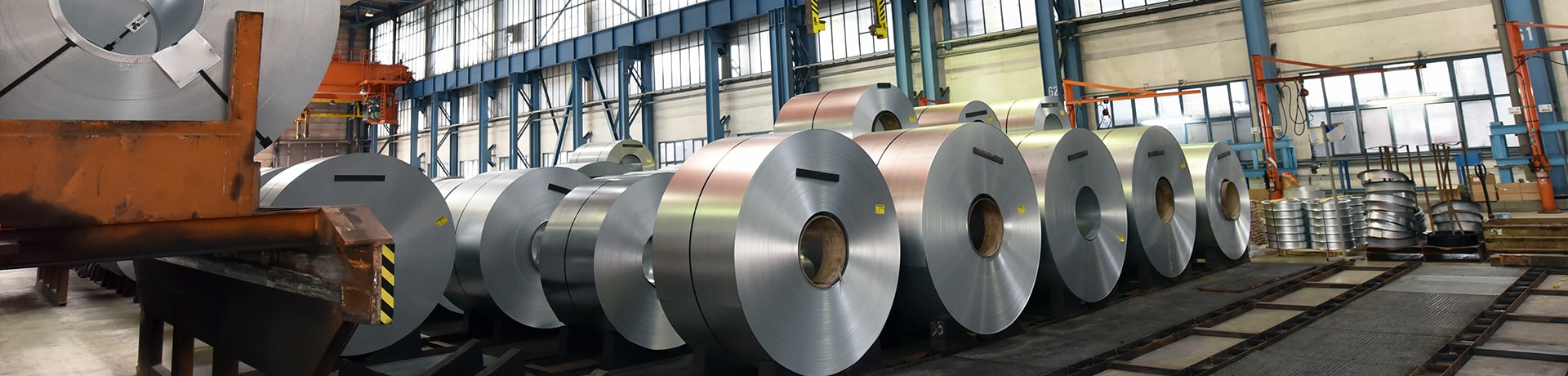
Introduction
Metal finishing plays a crucial role in manufacturing, enhancing the durability, functionality, and appearance of metal components. At Karas Plating, we specialise in high-quality metal finishing solutions, ensuring components meet strict performance and reliability standards.
This guide explores Karas Plating’s metal finishing processes, applications, key benefits, and how to choose the best solution for your needs. We’ve also included links to in-depth resources to help you understand the technical aspects of metal finishing.
What is Metal Finishing?
Metal finishing refers to a range of chemical, electrical, and mechanical processes applied to metal surfaces to enhance their corrosion resistance, conductivity, wear resistance, aesthetics, and durability. It can also be referred to as surface coating, surface finishing, metal plating, or surface treatment. It forms part of surface engineering and is usually an integral step of the manufacturing process.
It’s More Than Just Corrosion Prevention
While corrosion prevention is a vital function of metal finishing, it is important to recognise that the benefits extend far beyond this aspect. Metal finishing addresses various global challenges and provides immense value to society.
Processes like silver plating are crucial in reducing the risk of infection and disease. Metal finishing supports sustainability and technological innovations, which is key in advancing electric vehicles (EVs) and battery development.
Furthermore, it enhances artistic expression by improving the durability and visual appeal of metal artworks. In essence, the significance of metal finishing encompasses a wide range of applications that contribute positively to multiple fields, demonstrating its importance in today’s world beyond just corrosion prevention.
How does it work?
Metal finishing involves various techniques to alter the metal’s surface properties. Electroplating is one common method, where metal ions are deposited onto the base metal through electrolysis in a plating bath. The specific steps and methods used can vary significantly depending on the type of metal, the components being treated, and individual customer requirements. Post-treatment processes may also be applied to enhance the final product’s quality and longevity.
Base Metals (Substrates)
Base metals are classified as nonferrous metals, which do not contain iron, and are distinct from precious and noble metals. Metal finishing is a versatile process that can be applied to a wide array of base metal substrates such as:
- Nickel
- Aluminium
- Copper
- Zinc
- Tin
- Rhodium
- Cadmium
- Brass
- Stainless Steel
- Carbon steel
- Inconel
- Cuponal
Base metals are generally classified as common and affordable, in contrast to precious metals such as gold, silver, platinum, and palladium, which tend to be more expensive. One notable characteristic of base metals is their susceptibility to corrosion, oxidation, and tarnishing, particularly when exposed to environmental elements. To enhance their durability and appearance, metal finishing processes can be highly beneficial for these types of metals.
Corrosion Resistance
Prevents rust and oxidation, extending the lifespan of components exposed to harsh environments.
Improved Conductivity
Enhances electrical performance, reducing resistance in electronic and power distribution components.
Enhanced Wear Resistance
Protects components from mechanical stress, friction, and degradation over time.
Aesthetic Appeal
Achieves a smooth, uniform, or decorative finish suitable for industrial and consumer applications.
Better Adhesion for Coatings
Prepares the surface for painting, adhesive bonding, or additional plating layers.
Cost
Metal finishing plays a crucial role in helping manufacturers and end-users manage costs and improve cost efficiency in several ways:
Improving Durability and Reducing Operating Costs
For applications that experience frequent wear and breakdown of components, metal finishing is an effective solution to improve durability. This enhancement can lead to lower operating costs, reduced downtime, and long-term savings.
Processes such as plating and coating can significantly increase the durability of components, decreasing wear and tear and minimising the need for frequent replacements. This ultimately results in lower operating expenses and less downtime, which is particularly advantageous for applications with a high turnover of components. For example, zinc plating offers corrosion resistance, extending the lifespan of components and lowering maintenance costs.
Balancing Desired Finish with Cost:
Manufacturers need to find a balance between achieving the right look for their products and keeping costs down. For instance, while silver and gold are often seen as the top choices for finishes, companies can consider using more affordable options like tin and nickel.
These alternatives can still provide many of the same benefits as gold and silver but at a lower price, which is especially important for businesses that produce large quantities of items where every penny counts.
Types of Metal Finishing
Karas Plating offers a wide range of electroplating, electroless plating, and chemical treatments, each tailored to specific industry needs.
1. Electroplating
Electroplating involves using an electric current to deposit a thin layer of metal onto a substrate, enhancing its corrosion resistance, conductivity, and mechanical properties.
Below are the key types of electroplating offered by Karas Plating, with common industry applications.
Silver Plating
Silver plating is widely used for its exceptional electrical conductivity, corrosion resistance, and solderability, making it a top choice for electronic, aerospace, and automotive applications.
Common Applications:
- Busbars & Electrical Connectors – Used in power distribution systems, silver plating ensures efficient electrical conductivity and low resistance.
Read: Silver Plating Busbars – A Silver Lining
- Medical Equipment – Offers antimicrobial properties, making it suitable for surgical instruments and medical implants. Read: The Benefits of Silver Plating in the Medical Industry
- Aerospace & Automotive Components – Helps reduce friction, improve conductivity, and prevent oxidation in high-performance applications.
Read: Silver Plating in Aerospace Applications
Explore Our Silver Plating Services
Gold Plating
Gold plating is widely used in electronics, aerospace, and medical sectors, thanks to its superior corrosion resistance and conductivity.
Common Applications:
- Electronic Connectors & Circuit Boards – Gold plating prevents oxidation and degradation of electrical contacts, ensuring long-term reliability in high-performance applications.
Read: Advantages of Gold Plating in Electrical Connectors - Medical Devices – Due to its biocompatibility, gold plating is used in pacemakers, implants, and surgical tools to prevent reactions in the body.Read: Heart of Gold – Gold Plating in the Medical Industry
- Luxury Goods – Provides a decorative and corrosion-resistant finish for jewellery, watches, and high-end automotive interiors.
Explore Our Gold Plating Services
Copper Plating
Copper plating is widely used as an undercoat or standalone finish, offering excellent conductivity, corrosion resistance, and adhesion properties. It is particularly beneficial for electrical components, industrial machinery, and engineering applications.
Common Applications
- Electrical & Electronic Components – Copper’s high conductivity makes it ideal for circuit boards, busbars, and connectors.
- Heat Sinks & Thermal Applications – Used in electronics and industrial machinery to improve heat dissipation.
- Engineering & Plating Undercoats – Enhances adhesion for subsequent plating layers, such as silver, tin, or gold.
- Petrochemical Industry – High-build copper plating protects components in harsh offshore and marine environments.
Read: The Importance of High-Build Copper Plating in the Petrochemical Industry - Steel Hardening – Used in precision engineering to create a barrier layer before heat treatment.
Read: Hardening Steel with Copper Plating
Karas Plating offers precision copper plating for demanding applications, ensuring a uniform, high-quality finish.
Learn more about our Copper Plating Services
Tin Plating
Tin plating is a versatile metal finishing process used to enhance corrosion resistance, solderability, and conductivity. It is widely applied in electronics, automotive, and food processing industries. Karas Plating offers both bright and dull tin plating, each suited to different applications.
Bright Tin Plating
Bright tin plating provides a shiny, reflective finish, offering excellent solderability and corrosion resistance, making it ideal for electronic and electrical applications.
Common Applications:
- Printed Circuit Boards (PCBs) – Prevents oxidation, ensuring reliable soldering.
- Connectors & Terminals – Maintains low-resistance connections in electrical and automotive systems. Read: A Bright Idea – The Importance of Bright Tin Plating in the Electrical Industry
- Food Processing Equipment – Provides a non-toxic, food-safe coating that prevents contamination and corrosion.
Explore Our Bright Tin Plating Services
Dull Tin Plating
Dull tin plating produces a matte finish, offering excellent solderability while reducing whisker growth—a common issue in high-reliability electronic applications. It also provides better lubricity in mechanical components, making it useful for industrial and electrical applications.
Common Applications:
- Power Distribution Components – Used where low-resistance electrical connections are required.
- Mechanical Parts – Reduces friction and enhances wear resistance.
- Aerospace & Automotive – Preferred for components needing enhanced corrosion protection without high reflectivity.
Explore Our Dull Tin Plating Services
Zinc Plating
Zinc plating is primarily used for corrosion protection, forming a protective barrier on steel and iron components.
Common Applications:
- Automotive Industry – Protects steel components and fasteners from environmental damage.
- Industrial Machinery – Extends the lifespan of tools and mechanical parts exposed to moisture or chemicals.
Explore Our Zinc Plating Services
Passivation in Zinc Plating
Passivation is commonly used after zinc plating to:
- Enhance corrosion resistance
- Provide colour options (clear, yellow, black)
- Increase durability with additional sealing
- Can be applied in clear, yellow, or black finishes for added protection or aesthetics.
2. Electroless Plating
Unlike electroplating, electroless plating does not require an electric current. Instead, it uses a chemical reaction to deposit a uniform layer of metal onto a substrate. This makes it ideal for coating complex geometries and non-conductive surfaces, ensuring even coverage across all parts of the component.
Karas Plating specialises in Electroless Nickel Plating, which provides exceptional wear resistance, corrosion protection, and uniform thickness across intricate components.
Key Benefits of Electroless Plating
Uniform Coating – Unlike electroplating, electroless plating ensures a consistent metal layer thickness over the entire surface, even on complex shapes or internal cavities.
Superior Corrosion Resistance – Electroless nickel plating offers outstanding resistance to oxidation, chemicals, and extreme environments, making it perfect for aerospace, marine, and oil & gas applications.
Enhanced Wear Resistance – It significantly reduces friction and wear, increasing the lifespan of components subjected to high mechanical stress.
No Need for Electric Current – Since the process is chemical-based, it can be applied to non-conductive materials or intricate designs that may be difficult to electroplate.
Can Be Heat-Treated for Added Hardness – Post-plating heat treatment can further enhance surface hardness, making the component more resistant to wear.
Common Applications of Electroless Nickel Plating
Aerospace Components – Used in aircraft parts, engine components, and landing gear for its wear resistance and corrosion protection.
Oil & Gas Industry – Protects valves, pumps, and drilling equipment from extreme conditions and corrosive environments.
Automotive Engineering – Ensures durability in gears, pistons, and fuel injection systems where parts are exposed to friction and harsh conditions.
Electronics & Precision Engineering – Provides conductivity and protection in circuit boards, connectors, and industrial sensors.
Read: Electroless Nickel vs. Electrolytic Nickel Plating
Explore Our Electroless Nickel Plating Services
3. Chemical Conversion Coatings
Chemical conversion coatings enhance corrosion resistance, adhesion, and conductivity by chemically modifying the surface of metals. Unlike electroplating or electroless plating, these coatings do not deposit a separate metal layer but instead alter the surface structure to provide protection.
Iridite NCP – RoHS-Compliant Aluminium Conversion Coating
Iridite NCP is a non-chrome passivation process for aluminium and aluminium alloys, offering superior corrosion resistance while being fully RoHS compliant. Unlike traditional chromate conversion coatings, it contains no hexavalent chromium, making it an environmentally friendly alternative to treatments like Alocrom 1200.
Key Benefits
- Corrosion Resistance – Protects aluminium against oxidation and wear.
- Adhesion Promotion – Improves bonding for paints, adhesives, and additional coatings.
- Environmentally Friendly – Hexavalent chromium-free, meeting RoHS compliance.
- Retains Electrical Conductivity – Ideal for electronics and aerospace applications requiring conductive properties.
Common Applications
Aerospace & Defence – Used on lightweight aluminium components for long-term corrosion resistance.
Electronics & Precision Engineering – Enhances electrical conductivity while preventing surface degradation.
General Industrial Use – A preferred chromate-free alternative for paint adhesion and corrosion protection.
Karas Plating provides Iridite NCP as a sustainable alternative to traditional chromate coatings.
Read more: Choosing Iridite NCP Over Alocrom 1200
View the service page: Iridite NCP
4. Passivation Of Stainless Steel
Passivation is a chemical treatment that enhances corrosion resistance by forming a thin, protective oxide layer on stainless. It removes surface contaminants and acts as a barrier against oxidation, rust, and environmental damage.
How Passivation Works
- The metal is cleaned and treated to remove impurities.
- A chemical passivation solution forms a stable protective layer.
All passivates used at Karas Plating are hex-free and RoHS compliant, ensuring an environmentally friendly alternative to older cadmium-based processes.
Learn more: Zinc Plating & Colour Passivation
5. Zinc & Manganese Phosphating
Phosphating is a conversion coating that applies a thin crystalline layer of zinc or manganese phosphate to the surface of ferrous metals such as steel and Iron. This layer improves corrosion resistance, reduces friction, and enhances adhesion for subsequent coatings, such as paint or lubricants. There is a different process for aluminium.
There are two main types of phosphating:
- Zinc Phosphating – Primarily used as a pre-treatment for painting and powder coating, providing strong adhesion and corrosion resistance.
- Manganese Phosphating – Ideal for wear-resistant coatings in high-friction environments, as it retains oils and lubricants, making it perfect for automotive and industrial components.
Common Applications:
- Automotive Industry – Used in engine parts, suspension systems, and fasteners to protect against corrosion and reduce metal-to-metal wear.
- Defence – Essential for military equipment, where phosphate coatings prevent rust and improve durability in extreme conditions.
- Machinery & Tools – Enhances the performance of drill bits, cutting tools, and industrial fasteners by reducing friction and wear.
6. Other Metal Finishing Techniques
There are a variety of other metal finishing processes and techniques; these include:
Anodising
Anodising is an electrochemical process that enhances aluminium’s natural oxide layer, improving durability, corrosion resistance, and wear resistance. It works by coating the base metal with a protective oxide layer by an electrolytic process in which the metal forms the anode. The most common base metal for this is aluminium.
Common Applications:
- Architectural Fixtures & Decorative Aluminium – Used in cladding, window frames, and lighting reflectors for a clean, mirror-like finish.
- Consumer Goods: enhance the performance and appearance of electronic products and appliances, including smartphones, laptops, furniture hardware, and various household appliances. Its applications extend to improving durability, aesthetic appeal, and providing robust frames and structures.
- Aerospace & Automotive Components – Ensures that lightweight aluminium parts resist tarnishing, wear, and surface degradation.
Learn more: Anodising.
Galvanising
Galvanising is the process of applying a protective zinc coating to steel or iron, to prevent rusting.
Powder coating
For a durable finish, dry powder is electrostatically baked on the substrate
Mechanical Finishes
Mechanical finishes are mainly used to smoothen surfaces. They involve polishing, buffing, grinding, brushed finishing, blasting, and metal grinding. We provide clients with a range of blasting processes as an extension of our electroplating service.
Chemical Brightening
Chemical brightening is a specialist aluminium finishing process that improves the reflectivity, smoothness, and appearance of the metal while enhancing its hardness. Unlike mechanical polishing, which may create surface irregularities, chemical brightening delivers a consistent, high-gloss finish by dissolving the top layer of aluminium in a controlled chemical reaction.
Engineered Paints
Special coatings that enhance surfaces and provide chemical and corrosion resistance. These are especially useful to the oil and gas industry as they provide protection to facilities.
Heat Treatment
Often a critical stage in surface coatings and engineered paints, heat treatment is used to cure coatings. It can alter the properties of the substrate, improving characteristics such as resistance to corrosion and strength. Some common types of heat treatments available are annealing, tempering, quenching, and hardening, but there are plenty more treatment methods manufacturers can choose from.
Tinning
Tinning involves coating a substrate with tin; the main focus is applying or repairing a tin coating, which enhances the durability, functionality, and aesthetic appeal of components. This technique serves several purposes and is commonly used in soldering applications.
Metal Spraying
Metal spraying, or thermal spraying, is a surface engineering process where molten or semi-molten materials are sprayed onto a surface to form a protective coating. It works by heating a coating material—typically in wire or powder form—using a flame, arc, or plasma, then propelling it onto the substrate using compressed air or gas. This technique effectively enhances corrosion resistance, wear resistance, and thermal performance. However, the coating can be relatively porous and less uniform than electroplating, and the process may not be ideal for fine, intricate components. Electroplating often provides a denser, more even finish with stronger adhesion on detailed geometries—offering a more controlled and cost-efficient solution for many industrial applications.
Physical Vapour deposition
A vacuum-based coating process that enhances surface properties like hardness, wear resistance, and corrosion protection by vaporising and depositing a thin film onto the component. While it’s effective for decorative finishes and high-performance parts, it can be costly, time-consuming, and less suitable for complex shapes or large-scale production. Electroplating, on the other hand, offers similar protective benefits with greater flexibility, better coverage on intricate shapes, and more cost-effective scalability—making it a more practical choice for many manufacturers.
Vitreous Enamelling
Vitreous enamelling is a process where powdered glass (vitreous enamel) is fused to a metal surface by firing at high temperatures—typically around 800°C. This creates a hard, smooth, and often decorative coating that’s chemically bonded to the substrate, commonly steel or cast iron. While it offers excellent resistance to corrosion, heat, and chemicals, vitreous enamel can be brittle and prone to chipping under mechanical stress. For applications that demand a more impact-resistant and versatile finish—especially on complex or high-volume components—electroplating provides a durable, cost-effective alternative with broader industrial use.
Selecting The Right Metal Is Crucial
As you can see, many choices are available for base metals and finishing processes. Because of this, we always recommend carefully selecting the right combination of base metal and finishing process. This is crucial for ensuring your components perform optimally in their intended applications.
Many think it’s just about looks, but it’s more than just a question of aesthetics—it’s a strategic decision that impacts product quality, durability, cost-effectiveness, and compliance. Get it wrong, and the consequences can be financially and reputationally costly.
Surface Preparation in Metal Finishing
Proper surface preparation is essential for achieving high-quality, durable finishes. It ensures that contaminants, oxidation, and residues are removed, allowing for better adhesion, improved corrosion resistance, and a flawless final finish. It is a vital stage of the metal finishing process, as quality is everything in metal plating.
Karas Plating operates a dedicated surface preparation facility, using advanced cleaning and pre-treatment techniques to ensure consistent, high-performance results. We deeply understand that the performance and quality of electroplated substrates depend upon the surface cleanliness.
1. Why Surface Preparation is Important
Before any metal finishing process, components must be thoroughly cleaned to remove contaminants such as oil, grease, dirt, and oxidation. Without proper preparation, plating may not adhere correctly, leading to:
- Blistering or peeling coatings
- Uneven finishes and rough textures
- Compromised corrosion resistance
Karas Plating’s specialist pre-treatment processes help eliminate these risks, ensuring consistent and durable plating results.
Read more about Karas Plating’s Surface Preparation Processes
2. Surface Preparation Processes
To ensure high-precision, reliable surface preparation, Karas Plating uses a range of specialist cleaning and blasting processes, each suited to different component requirements.
Tunnel Blasting
A high-volume automated process that rotates components to achieve uniform surface cleaning. Ideal for larger parts requiring thorough pre-treatment before plating.
Hand Blasting
A manual blasting process that allows for precise cleaning of delicate or intricate components. Often used for aerospace, electronics, and semiconductor components where precision is critical.
Aqua Blasting
A water-based process that cleans and blasts components simultaneously, providing a smooth, contaminant-free surface. Less abrasive than dry blasting, making it ideal for replating or components requiring a uniform finish.
- Often used for rail components and outdoor parts exposed to dust, grease, and environmental contaminants.
- Removes debris and prepares materials for a high-quality, long-lasting finish.
Degreasing & Cleaning
A process designed to remove oils, lubricants, and organic contaminants from surfaces, ensuring plating consistency and durability.
- Karas Plating uses an industrial degreasing system, including a dishwasher unit, to efficiently clean hollow components and intricate parts.
3. How Surface Preparation Enhances Plating Quality
A well-prepared surface enhances plating performance by:
Improving Adhesion – Ensures the plating bonds effectively, reducing peeling or blistering.
Reducing Surface Defects – Minimises pitting and inconsistencies in the coating.
Enhancing Corrosion Resistance – Creates an optimal surface for long-term protection.
Achieving a Smooth Aesthetic Finish – Provides a uniform and visually appealing surface, valuable for automotive, medical, and electronics applications.
Karas Plating’s dedicated pre-treatment facility ensures reliable, high-quality plating results across all industries.
Read more about Karas Plating’s Surface Preparation Facility
Metal Finishing Quality Standards & Compliance
Why Quality Standards Matter in Metal Finishing
Metal finishing plays a critical role in ensuring that components meet performance, safety, and durability requirements across industries such as aerospace, automotive, medical, and electronics. Strict quality control and regulatory compliance are essential to guarantee consistency, reliability, and longevity in finished components.
Certifications such as ISO 9001, RoHS compliance, and aerospace or medical industry approvals ensure that plating processes meet global industry standards. These certifications help manufacturers reduce product failure rates, improve corrosion resistance, and ensure compatibility with strict environmental and safety regulations.
Key Industry Standards & Certifications
ISO 9001: Quality Management Systems
ISO 9001 is a globally recognised quality management standard, ensuring that manufacturers follow consistent, repeatable, and well-documented processes to maintain high production standards.
ISO 14001: Environmental
We are dedicated to making a positive difference by minimising the environmental impact of our comprehensive range of electroplating, surface coating, and metal finishing services. Through our unwavering efforts, we have successfully reduced emissions and effluents, benefiting our clients and the planet.
Approved to ISO 14001 (Environmental)
Read more about Karas Plating’s Quality Commitment & Accreditations
RoHS & REACH Compliance: Environmental & Safety Regulations
- RoHS (Restriction of Hazardous Substances) ensures that metal finishing processes do not contain banned hazardous materials, making coatings safe for electronics, automotive, and consumer goods.
- REACH (Registration, Evaluation, Authorisation, and Restriction of Chemicals) regulates chemicals used in plating to protect human health and the environment.
Karas Plating maintains full RoHS and REACH compliance to ensure all processes align with the latest environmental and safety regulations.
Read more about Karas Plating’s Environmental Responsibility
Industry-Specific Compliance & Testing
Different industries require specialised plating standards to meet unique performance demands:
- Aerospace & Defence – High-reliability coatings for electrical connectors, aircraft components, and fasteners.
- Medical & Healthcare – Biocompatible finishes for surgical instruments, implants, and medical electronics.
- Automotive & Electronics – Corrosion-resistant and conductive coatings for busbars, circuit boards, and electrical connectors.
Industry-Specific Compliance & Testing
Many Industry bodies and trade associations represent metal finishing and support businesses within the sector. They act as a collective voice, advocating for industry interests with governments and policymakers while establishing standards and best practices. In the UK, these include:
How Karas Plating Ensures Compliance & Quality
At Karas Plating, we are ISO 9001:2015 certified, ensuring rigorous quality control across all processes. We also maintain full RoHS and REACH compliance, meeting strict environmental and safety standards.
To guarantee precision and performance, our quality testing can include:
- X-ray Fluorescence (XRF) Testing – Ensures accurate plating thickness.
- Adhesion & Hardness Testing – Verifies durability and wear resistance.
- Salt Spray & Corrosion Resistance Testing – Assesses protection against harsh environments.
By adhering to global quality standards, Karas Plating provides high-performance metal finishing solutions that meet the strictest industry requirements for safety, reliability, and longevity.
Why Choose Karas Plating?
With over 70 years of expertise, Karas Plating delivers high-quality electroplating, electroless plating, and chemical treatments, ensuring precision and reliability.
What Sets Us Apart?
- Advanced Facilities – State-of-the-art plating for components of all sizes.
- Custom Solutions – Tailored finishes to meet specific requirements.
- Quality & Compliance – Adhering to ISO standards, RoHS compliance, and aerospace regulations.
- Reliable Delivery – Fast turnaround to keep your operations on track.
- Sustainable Practices – Eco-friendly plating with efficient resource management.
Partner with Karas Plating
Karas Plating delivers precision, durability, and full compliance with industry standards. Whether you need electroplating, electroless plating, or specialist coatings, we provide tailored solutions to meet your exact specifications.