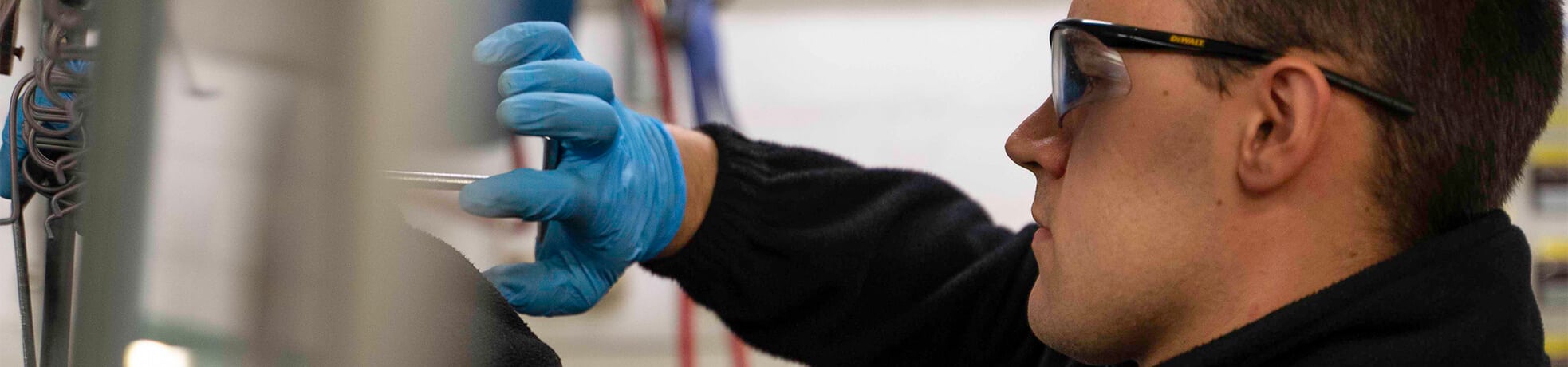
There are two main ways to plate your components with nickel – electrolytic and electroless – but which is better? In this article, we’re going to look at the two nickel plating techniques and their respective benefits.
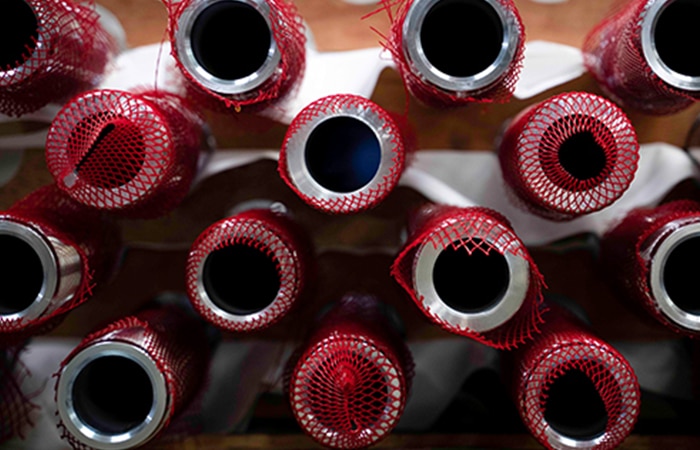
What is electrolytic nickel plating?
Electrolytic nickel plating is a form of electroplating, where the substrate is submerged into a bath containing a base solution and positively charged nickel. A negative current is passed through the parts that are suspended in solution attracting ions from a positive anode, forming a circuit between the nickel and the substrate. Ions are released from the nickel, which then attach themselves to the surface of the substrate.
Benefits of electrolytic nickel plating
While generally not as popular as electroless nickel plating, the electrolytic process does have a couple of advantages. These include:
Nickel Purity
You can use 100% nickel when plating with the electrolytic method, unlike the electroless technique, which requires the addition of phosphorus. This means that the deposit is slightly better at conducting electricity and has an improved level of heat-resistance.
Scalability
Electrolytic nickel plating tends to be cheaper than electroless nickel plating and the process itself is quicker. This lends itself well to higher volumes of production, particularly if uniformity and precision of plating are less important.
What is electroless nickel plating?
Electroless nickel plating also involves submerging the substrate in a bath of solution. This time the solution contains dissolved nickel phosphorus. When the substrate is submerged, the positively-charged nickel ions are automatically drawn to it and deposited evenly across its surface.
Benefits of electroless nickel plating?
Electroless nickel plating offers several notable advantages over the electrolytic process, which makes it such a clear choice in numerous industries. These include:
Uniformity
Electroless nickel plating delivers more precise results than electrolytic nickel plating and can be used to plate intricate and complex substrate components.
Corrosion resistance
Thanks to the phosphorus in the solution, electroless nickel plating offers improved resistance to corrosion.
EMI Shielding
Likewise, the inclusion of phosphorus gives the plating magnetic properties that can help to limit electromagnetic interference – a major benefit for the electronics industry.
Hardness and durability
Nickel deposits from this process can be heat-treated to improve their hardness, with certain low-phosphorus coatings reaching as high as 63 Rc on the Rockwell hardness scale.
Lubricity
Electroless nickel plating has enhanced lubricity, creating less friction when rubbing against other materials, reducing the risk of surface scarring.
Ductility
Electroless nickel plating is far more ductile than electrolytic nickel plating, making it less likely to shatter, break, or crack under stress.
Versatility
Not only can you apply electroless nickel plating to almost any metal substrate, the process allows you to increase the thickness of the plating as much as you like.
What is the best process for me?
Both methods result in a thin layer of nickel being added to the target substrate, but electroless nickel plating provides several notable advantages compared to the electrolytic process. Key among these are its improved wear- and corrosion-resistance, as well as its lubricity. Of particular importance to precision industries is that electroless nickel plating deposits the metal much more evenly across the components and can also produce a thinner layer, where needed.