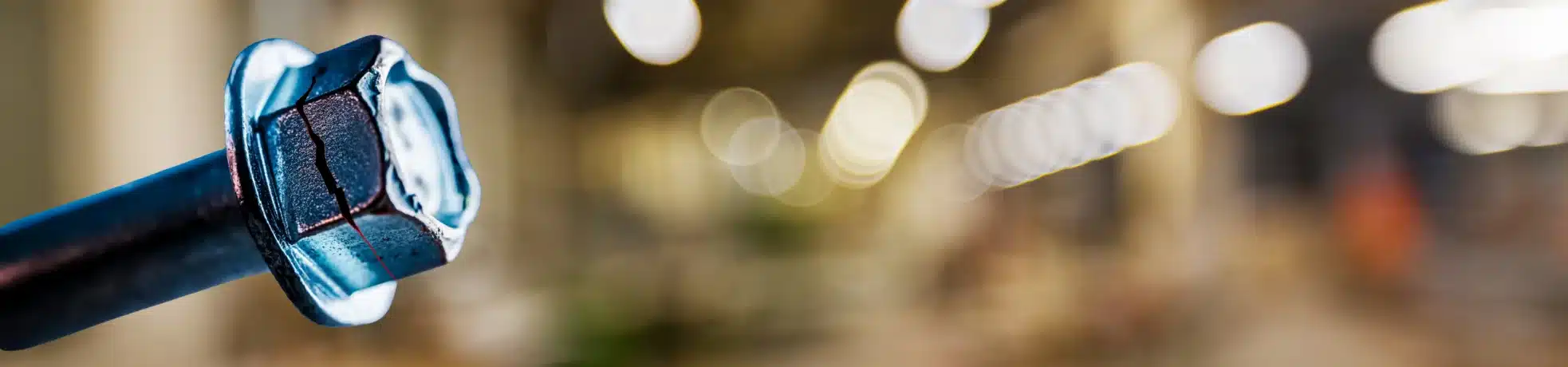
If you work with high-tensile steels, fasteners, automotive and aerospace parts, there’s one problem you can’t afford to ignore: hydrogen embrittlement. It can cause catastrophic failures in critical components, especially those under tensile stress or used in demanding environments.
What is hydrogen embrittlement?
Hydrogen embrittlement is a phenomenon in which the absorption of hydrogen into a metal, particularly high-strength steels, reduces its ductility and fracture toughness, rendering it more prone to brittle cracking and sudden failure.
Let’s take a look at what it is, why it happens, and what you can do about it.
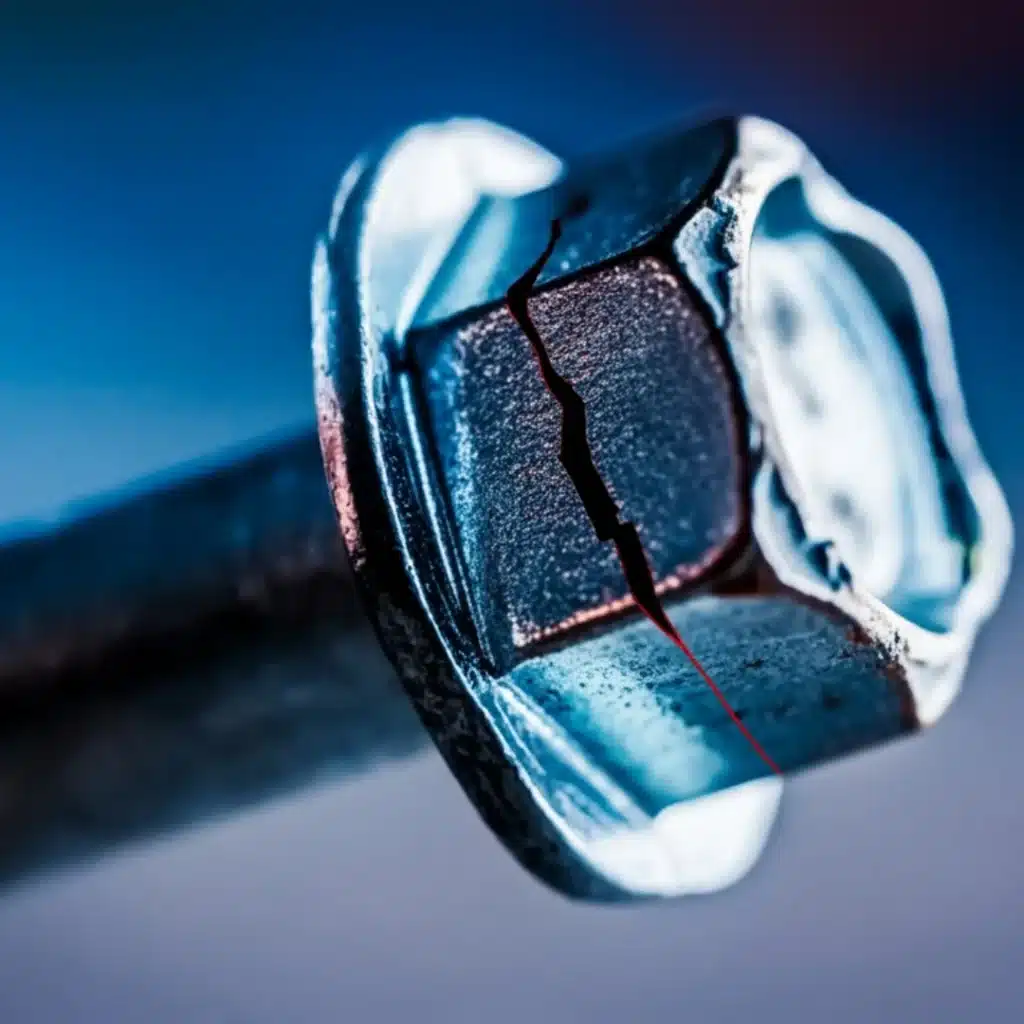
How it happens
Hydrogen atoms can diffuse into the metal from various sources, such as during manufacturing processes (like pickling or electroplating) or from in-life use, and accumulate at defects or grain boundaries, facilitating crack initiation and propagation.
The metal may appear fine on the surface, but beneath, it becomes brittle and is more likely to crack or break, especially under stress. There are usually no signs or notice when this might happen, making it more difficult.
Which materials are most at risk?
Not all metals are equally affected. Hydrogen embrittlement is mostly a problem for:
• High-tensile steels (like fasteners used in heavy-duty applications)
• Spring steels
• Nickel alloys under high fatigue
• Titanium and aluminium alloys, depending on the environment
At Karas, we regularly see signs of fatigue and cracking in stressed components that haven’t been protected against this risk, especially in industries that push their materials to the limit, like nickel alloys.
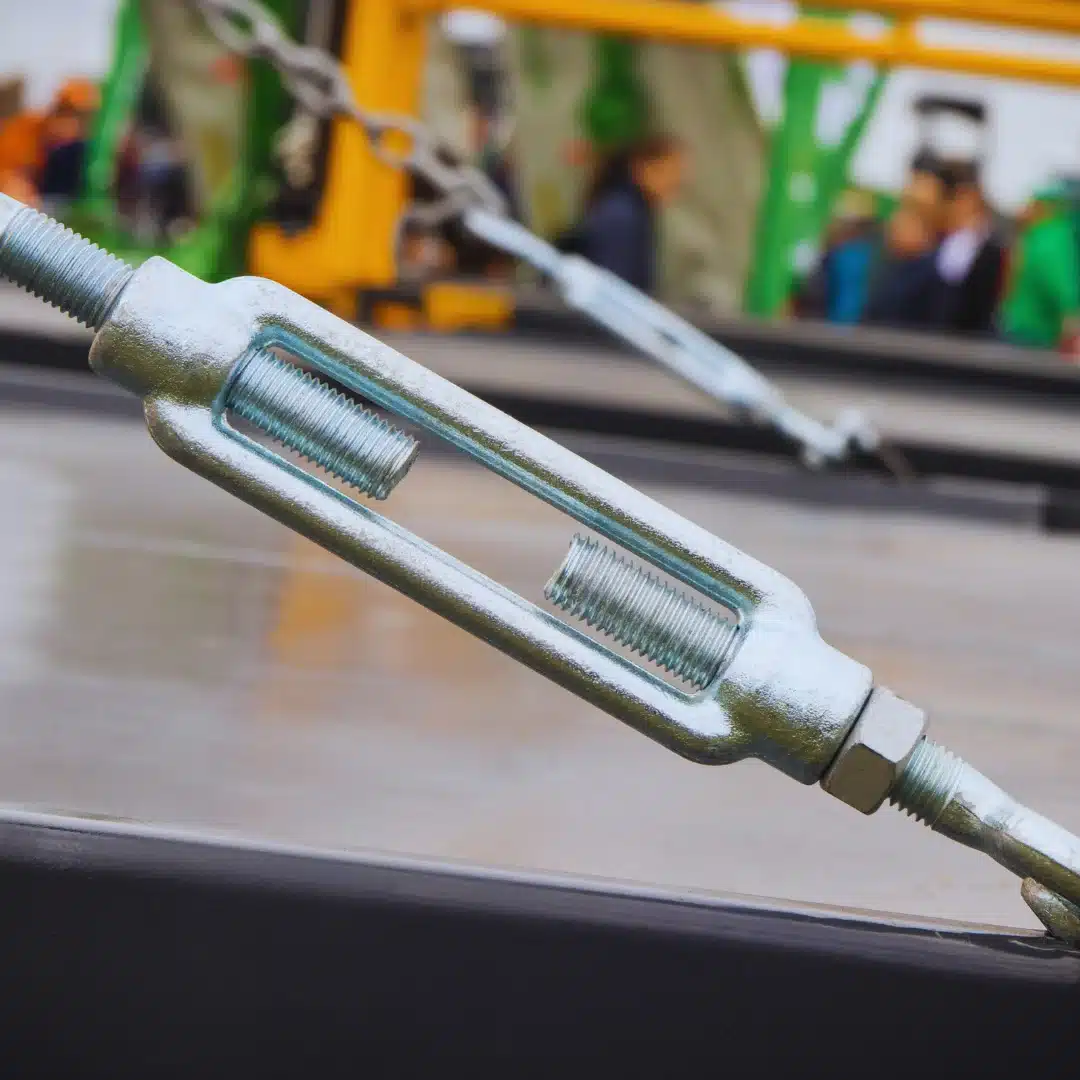
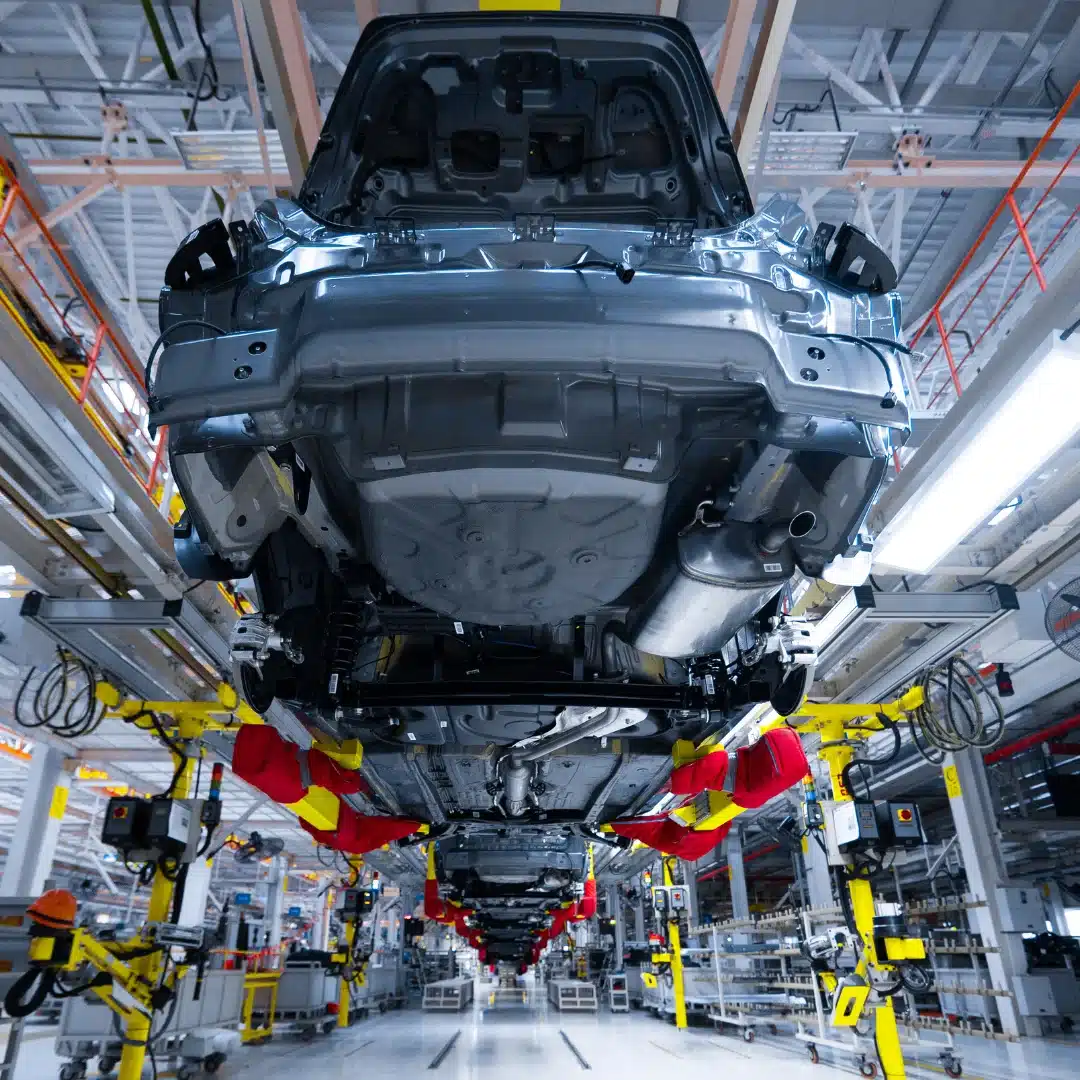
Who’s most affected?
This is a big concern across several industries, especially:
• Automotive
• Petrochemical
• Energy
• General manufacturing
If you use high-strength fasteners in machinery or critical systems, this applies to you. Parts used in bridges, vehicles, aircraft, and power plants that use high-strength steels or susceptible alloys are also affected.
Fasteners made from 10.9 or 12.9 grade steels are particularly susceptible to failure, often occurring without warning. That’s why it’s so essential to consider hydrogen embrittlement from the start, before those parts go into service.
Why it’s a serious problem
A brittle fastener in the wrong place can lead to significant problems for both the supplier and the end user. Cracks can form over time, especially under load, and eventually the part snaps, which might take the whole system down with it. It could be a safety issue. It could stop production. Either way, it’s a big deal. Worse still, these failures often happen without warning. The part might pass inspection, go into service, and then give way days or even weeks later.
Consequences
The consequences of hydrogen embrittlement are major. Safety hazards arise from sudden failures in critical systems whilst they are in use. Financially, unplanned downtime and recalls can cripple operations, while reputational damage erodes stakeholder trust.
Surface Preparation
Hydrogen embrittlement can be introduced during cleaning, especially if acid or alkaline treatments aren’t handled carefully. That’s why we take extra care during pre-cleaning, using a mix of blasting and surface preparation methods depending on the component.
Processes
Processes like tumble blasting remove flash and burrs from hard-to-reach areas, while phosphate coatings can help prevent problems before plating even starts. If you’re plating high-strength steels, post-baking after plating is also key. It helps remove any hydrogen that may have entered during the process. Not all plating companies offer this, but they should, especially when fasteners or structural components are involved.
It starts with knowing your application.
One of the best ways to reduce the risk of hydrogen embrittlement is to understand where and how your component will be used. For example, copper is often used in electrical systems not only for its excellent conductivity, but also because it doesn’t suffer from hydrogen embrittlement in the way high-strength steels do. In particular, oxygen-free copper is preferred in some applications because it can be welded without issues related to hydrogen absorption.
That kind of understanding helps guide both material selection and surface treatment choices from the outset.
Teamwork
Collaboration is important for reducing the risk of hydrogen embrittlement. When teams work together, they can share industry knowledge to better understand the mechanisms, prevention techniques, and industry standards necessary to ensure component reliability and safety.
Recognising the symptoms of hydrogen embrittlement is essential, however, affected components such as fasteners may look completely normal externally until they fail, making visual inspection alone insufficient for detection.
Conclusion
Hydrogen embrittlement may not be immediately apparent, but it can have significant consequences, ranging from failed bolts to compromised systems. For manufacturers and engineers working with high-tensile steels and fasteners, it’s something that needs to be planned for, not dealt with after things go wrong.