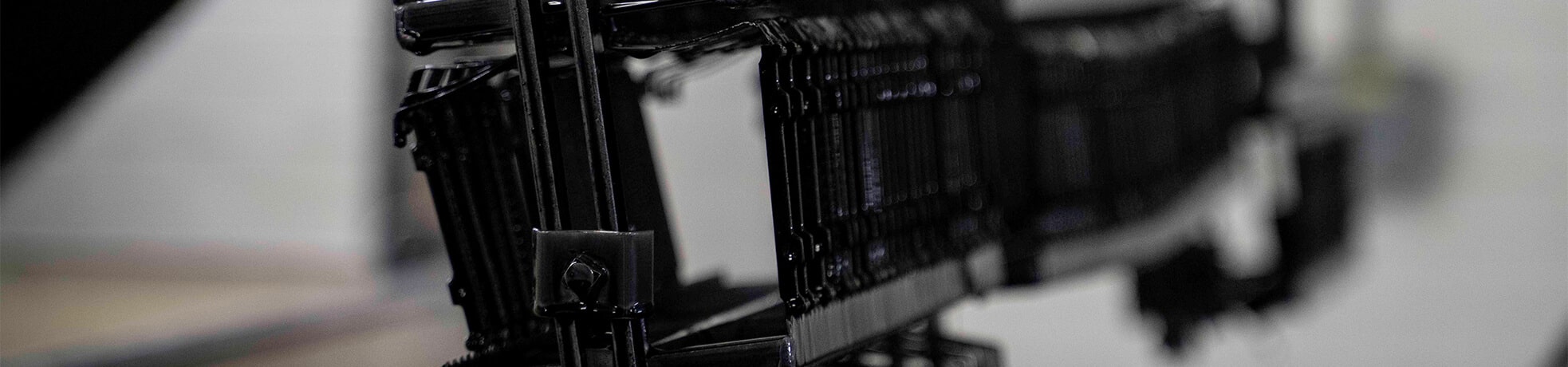
When we talk about the plating process, we tend to concentrate on the type of metal that we are depositing onto the substrate. However, it’s important to consider the base material itself and how it can affect the plating process and the finished product.
In this article, we are going to look at some of these substrate metals that are most popular among our plating clients and discuss their particular properties.
Aluminium
Aluminium is a popular base metal in many industries. It is lightweight, easy to cast, and has impressive structural strength. It can be 100% recycled, making it a good choice for companies keen to demonstrate their green credentials, and is an excellent conductor of heat. These properties make aluminium a common choice for the aerospace, telecommunications, medical, defence, and power generation sectors, among others. When plating onto aluminium, the substrate often needs an adhesive undercoat; otherwise, the base metal can oxidise during the process, preventing proper deposition.
Copper
Copper is used as both a substrate and a plating metal, making it a versatile material. It is the perfect material for conducting heat and electricity and is also highly malleable and ductile, making it suitable for many industrial applications. Common metal plating techniques used on copper substrates include tin plating (for improved solderability), silver plating (for improved electric conductivity), and nickel (for improved corrosion resistance and higher operating temperatures).
Carbon steel
Carbon steel is commonly used in many industries, being one of the cheapest and most prevalent forms of steel on the market. It’s a tough and durable material with low tensile strength that’s easy to form and weld. A major downside is that it is prone to rusting, making it essential to plate it with a corrosion-resistant metal, such as nickel. Carbon steel can be plated using electroless methods, which are often more cost-effective. Perhaps the most common plating method for carbon steel is zinc, another highly corrosion-resistant metal, although some industries (notably the automotive sector) are moving towards a zinc/nickel plating technique for improved resistance.
Stainless steel
While more expensive as a base material than carbon steel, stainless steel has many beneficial properties built-in. It is corrosion-resistant, has a high tensile strength, and is extremely durable, while also being easy to form and fabricate. Like aluminium, it can also be easily recycled. From a plating perspective, we use the same techniques for stainless steel as we would for any other substrate, though many clients prefer a coating of nickel prior to full plating for improved adhesion.
Titanium
Titanium is the strongest known metallic element and boasts superb corrosion resistance, making it a popular choice for high-temperature, high-stress environments, such as the aerospace industry, where it is employed in the manufacture of gas turbines and jet engines. It can be difficult to plate titanium since it is a highly active metal, and the combination of aqueous solutions, heat, and electrical current (all key components of the plating process) can cause it to oxidise, preventing the plate from sticking. We have to carefully prepare the substrate prior to plating to eliminate the risk of oxidation, as well as remove any surface contaminants that might lead to embrittlement.
Inconel
Inconel is trademarked name that refers to several nickel, chromium, and iron superalloys. Owned by the Special Metals Corporation, these high-performance alloys are used extensively in industries that operate in extreme environments, such as the oil and gas sector. This is due largely to their high resistance to oxidation and corrosion, making them perfect for undersea work. Since they are found in submarine environments, some of the most popular plating methods include copper plating, which helps to limit biological marine growth on the substrate, as well as silver plating, which allows for increased electrical and thermal conductivity.
If you’re curious about the base metals we plate on, visit our Base Metal Substrates Page to discover more. We provide detailed information on the various materials we work with, including their unique properties and common applications. Whether it’s silver, gold, or zinc plating, we offer solutions tailored to your specific needs.
In addition to our plating services, we also offer shot blasting and cleaning to ensure a pristine finish. If you don’t see your preferred metal listed, don’t hesitate to get in touch. Our team will be happy to discuss your requirements and find the best solution for your project.