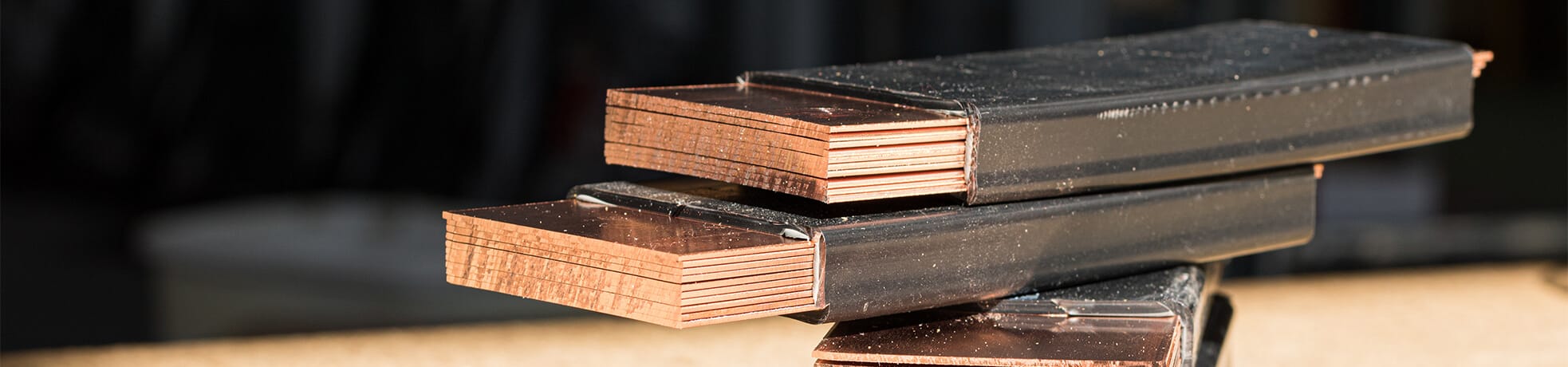
Benefits of Nickel Plating for Copper Busbars
In this article, we’re going to look at another popular finish for busbars—nickel plating—and see what benefits it can offer you and your company. Nickel plating offers several measurable benefits to its end users. These are some of the popular ones:
Improved durability: compared to copper, nickel is a much harder and more durable metal. By applying it to your copper busbars, you are adding a layer of protection that will resist wear and erosion – an important consideration if the busbars are in a high-vibration system.
Improved corrosion resistance: copper is highly reactive and prone to corrosion when exposed to humidity in the air. Nickel is much more resistant to corrosion, so a layer of nickel plating can significantly expand the lifespan of your copper busbars.
Improved wear resistance: if your copper busbars are fitted into a system that includes moving parts, they will be worn down over time, leading to shorts and power outages. Nickel plating is tough and durable, preventing this from happening so frequently.
Improved adhesion: nickel has excellent adhesive properties and is often used as a base layer for other metals such as gold and silver. In this instance, the nickel plating provides the protection required for long-lasting busbars, while the additional layer of silver or gold significantly improves conductivity and performance.
Reduced friction: nickel plating gives your copper busbars a low-friction surface, which limits the risk of electrical arcing in the system, particularly on components that are regularly inserted and removed, such as connectors.
Nickel Plated Busbar Use Cases
Automotive
Nickel plating is commonly used for busbars in the automotive sector, particularly in electrical and hybrid vehicles. It is essential for corrosion protection and less prone to rust, whilst maintaining an aesthetically pleasing look; giving a part the feel of a premium product. They are also common in the energy sector as they are used in a wide variety of power systems.
Electronics
According to the Nickel Institute, one of the biggest applications for nickel plating is on computer hard disc drives. Applying a thin layer of nickel to hard disc drivers provides much-needed resistance against corrosion and increases durability which is key when it comes to hard disk drives as people tend to keep their computers for a long time.
Aviation and Aerospace
Nickel is one of the electroplating methods in the aerospace sector due to its characteristic to withstand high temperatures, a common feature of aircraft operating conditions. Nickel electroplating has a variety of uses such as protecting parts from corrosion, joining components, and allowing them to be repaired instead of being completely discarded making the sector more environmentally friendly and reducing cost.
Nickel Plating vs. Electroless Nickel Plating
There are two main ways to deposit nickel on your copper busbars, and both offer their own advantages, depending on your particular specifications.
Nickel plating (or electrolytic nickel plating) involves submerging the substrate in a solution containing nickel ions that are then deposited onto the base metal when a charge is passed through the solution. It produces a uniform layer of nickel and can be adjusted by trained plating technicians to meet your particular specifications.
Electroless nickel plating (or ENP) does not require an electric current, relying on chemical reactions to deposit the nickel on the substrate. Electroless nickel plating allows us to apply an incredibly thin layer of nickel to your components, making it a popular choice for precision work. There is less control over the process than with electrolytic nickel plating, making it more straightforward to apply.