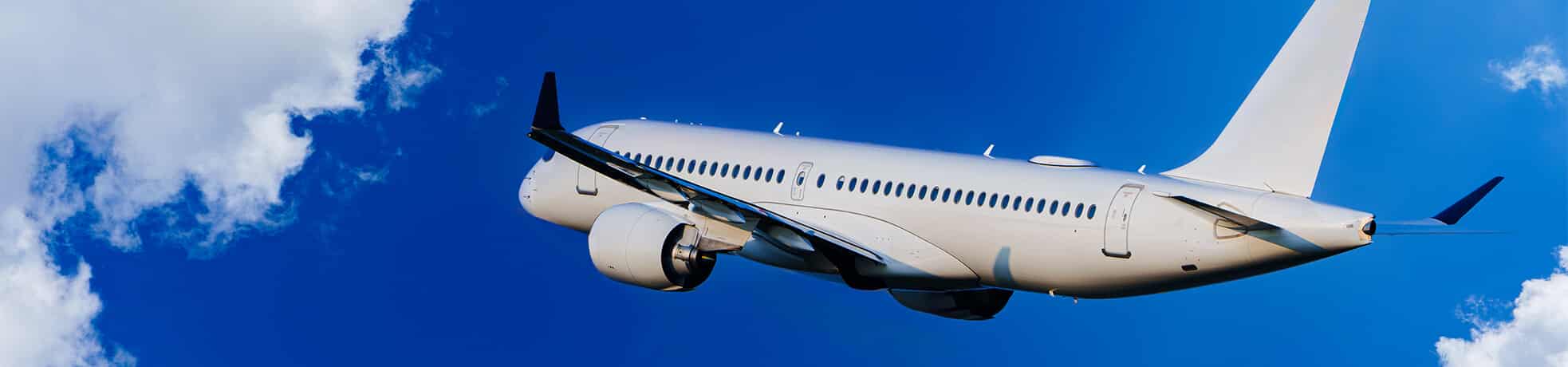
Busbars are the backbone of electrical systems in the aerospace industry, responsible for the distribution of power within a variety of mission-critical aircraft systems. In the demanding environment of aerospace applications, busbars must not only be reliable but also capable of withstanding extreme conditions without compromising performance.
In this article, we examine the importance of busbars to the aerospace industry and why quality busbar plating is essential.
What are Busbars used for in Aerospace?
Busbars are crucial for the distribution of electrical power across an aircraft. From the vital operations of engine controls, fuel systems and communication systems to in-flight entertainment and lighting, busbars ensure that every watt of power reaches its designated location efficiently and safely. They are designed to handle the complex load variations and the stringent safety requirements of the aerospace industry, providing a reliable power supply in both the cockpit and the cabin, and supporting the critical operations that keep aircraft in flight.
Aircraft rely on multiple busbar systems, which are independent of one another. In the event that one system fails, the aircraft can still draw power from the other systems. This redundancy is crucial to reducing the risk of failure and ensuring the safety of the aircraft and its passengers. The number of busbar systems used may vary depending on the type of aeroplane.
Why is Busbar Plating Important in the Aerospace Industry?
As with any high-performance sector, the aerospace industry relies on plating, surface coating, and metal finishing to ensure all components are manufactured to the highest possible standard.
In aerospace applications, busbar plating enhances functionality, efficiency, and safety. The unique stresses placed upon electrical systems in aircraft—such as rapid temperature changes, vibration, and the necessity for minimal weight—make the choice of busbar plating material crucial.
Increased Conductivity for Efficient Power Transfer
For aerospace busbars, high conductivity is vital. Silver plating is often used due to its excellent electrical conductivity, ensuring that power is transferred with minimal loss, which is essential for the efficient operation of the aircraft’s electrical systems.
Corrosion Resistance at High Altitudes
The high-altitude conditions that aircraft encounter can lead to an increased risk of corrosion due to moisture and other environmental factors. Electroless nickel plating is valued in the aerospace industry for its ability to resist corrosion, thereby maintaining the integrity of the busbar’s electrical connectivity over time.
Solderability for Secure Connections
In aerospace, where every connection point is critical, the solderability provided by certain plating materials, such as electroless nickel, can make a significant difference. A well-soldered joint is vital for maintaining uninterrupted power distribution during flight.
Heat Resistance and Thermal Management
The intense thermal stress on aerospace electrical components demands a plating solution that can withstand significant temperature extremes. In flight, the exterior of an aircraft faces sub-zero temperatures at high altitudes, while engine components, like the combustion chamber, can exceed 2000 degrees Celsius. Effective cooling systems play a part, but the right plating solution – such as silver or electroless nickel—is essential for busbars to maintain structural integrity and performance.
Durability Amidst Physical Stresses
Durability is crucial as aerospace busbars must endure the physical stresses of takeoff, flight, and landing. Plating adds a layer of protection, equipping busbars with the resilience to withstand these conditions and prolong their operational life. Applying a layer of nickel to busbars adds a layer of protection that resists wear and erosion – an important consideration in a high-vibration system. For high current connections, silver plated busbars perform better than unplated busbars by providing stable contact resistance and a low maximum operating temperature, therefore increasing the service life of the bus joint.
Optimal Power Flow
One of the main concerns in the distribution of electrical power is optimising flow, which can be achieved through low-resistance conductive joints. Field experience and laboratory studies have shown that this is particularly important in the case of busbars and bolted high-current connections. Unplated joints are generally less reliable due to the possibility of oxidation on the surfaces. In high-current applications like those involving busbars and bolted connections within aircraft electrical systems, plating or coatings are crucial in ensuring reliability. Unplated joints are more prone to oxidation, which can cause conductivity degradation and potentially lead to failures.
Karas Plating: Precision Plating Solutions for Aerospace
Quality Assurance for Aerospace Standards
We ensure that our busbar surface finishes adhere to strict quality standards, providing our clients with plating services that meet and exceed the rigorous certifications required for aerospace components.
All our busbar plating processes are fully approved to meet ISO 9001 standards for Quality and ISO 14001 standards for Environmental. This ensures a high standard of plating on all orders, plus an environmentally responsible approach to any waste material or by-products.
A Variety of substrate
We offer busbar plating solutions for a wide range of materials and designs for the aerospace sector:
Silver plating for busbars
Silver is a commonly used material in the aviation industry due to its numerous benefits, particularly in reducing the risk of galling at high temperatures. For busbars, silver plating provides excellent conductivity, making it an ideal choice for high-performance aerospace applications. Silver is soft, which allows it to be precisely applied to components, even those with curves or crevices, resulting in an improved finish quality and contact area. Some of our customers choose silver plating over tin to prevent whisker growth, which can cause short circuit failures and flashovers between adjacent busbars.
Electroless Nickel Plating for busbars
Nickel-plated busbars have a hard-wearing outer layer that is resistant to wear, oxidisation, and corrosion. This layer makes it easier to weld other components to the busbars, and they are highly popular for extending the durability of copper busbars. They are especially suitable for high-temperature applications, just like silver-plated busbars. They are particularly useful in aerospace applications where exposure to high temperatures, corrosive environments, mechanical wear due to vibration, contact with other surfaces, and maintenance of electrical components are concerns.
Tin Plating for busbars
Tin is an excellent alternative to copper busbars as it offers greater corrosion resistance and is less prone to corrosion than copper. The use of tin-plated busbars also offers aesthetic benefits, particularly when bright tin is used. Tin is the most cost-effective option; however, its application is limited due to the potential for tin whisker formation.
Gold plating for busbars
Busbars can be protected from chemical and mechanical damage by applying a layer of gold plating. This protective layer enhances the corrosion resistance of the busbars more than silver plating, but it does result in lower conductivity. Gold plating is commonly used in electrical conductors and connectors, although it can be quite expensive. In the aerospace industry, other metals may be more suitable than gold.
Copper plating for busbars
Copper plating of busbars offers several advantages over other electroplating methods. Similar to silver-plated busbars, it is highly conductive, with copper showing only slightly lower conductivity than silver in standardised testing. Copper plating provides a dependable and effective way to distribute electrical power within aircraft systems.
Which busbar coating is recommended for the aerospace industry?
When selecting a coating for busbars in the aerospace industry, it is essential to consider the numerous options available that align with the performance requirements and cost considerations of the application. At Karas Plating, we understand this critical decision-making process. Therefore, we offer our expertise to ensure that you select the most suitable coating for your aerospace components. Contact us for assistance in selecting or applying coatings for your busbars.
Electrical power systems are the future
The Aerospace Technology Institute has highlighted the growing significance of electrical power systems in present and future commercial aircraft. As a result, having a trusted plating partner for your busbars has become an indispensable consideration as the demand for superior technologies increases. Our expertise and impressive track record of helping suppliers speak for themselves. We are confident in our ability to deliver the highest quality product, ensuring you receive the best service possible. Choose Karas Plating, and let us help you deliver high-quality, high-volume parts consistently and efficiently.