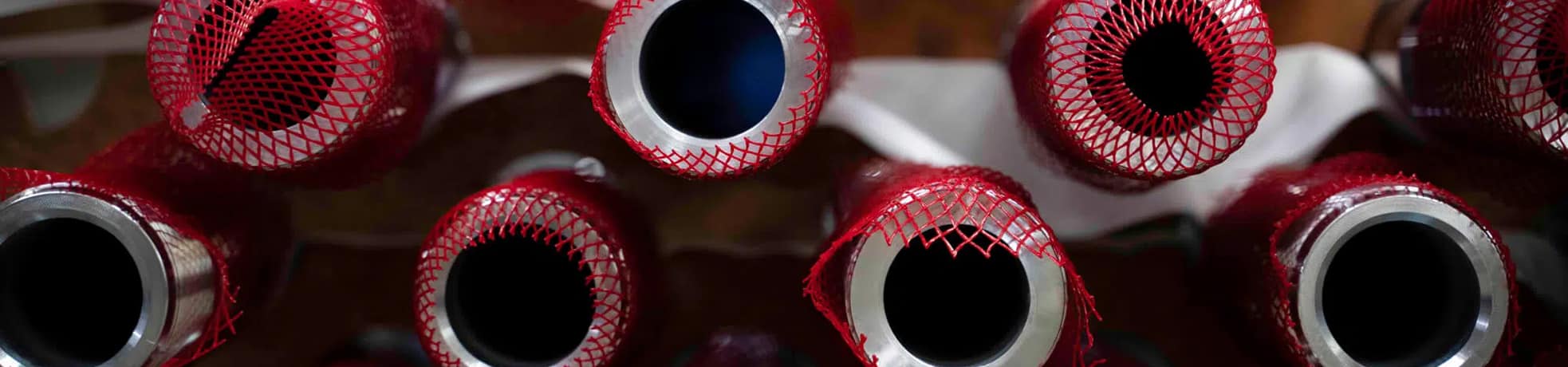
Electroplating is a versatile and valuable process in modern manufacturing and engineering. At Karas Plating, we specialise in a range of electroplating techniques, each offering unique benefits tailored to various industries.
Electroplating offers the significant advantage of imparting new and advantageous properties to metals. This capability is particularly valuable in various industries and applications where there is a need to enhance the properties of a substrate. Here, we explore the key advantages of electroplating and how our services can enhance your products.
Understanding the benefits of electroplating requires knowing its process, how it works, its uses, and its history. While it may seem like a modern technique, electroplating has been improving civilisation for over 200 years, with its principles dating back thousands of years. The idea of bonding one metal with another has been around for even longer, across thousands of years, in fact.
What is Electroplating?
Electroplating is a process where one metal is deposited over another in a liquid containing a metal salt. This process coats a material with a thin layer of another metal using electricity. Electroplating improves the appearance, durability, and resistance to rust of the base material. It is used in many industries to add both functional and decorative benefits.
What are the Key Advantages of Electroplating Processes?
Enhanced Corrosion Resistance
One of the primary benefits of electroplating is its ability to significantly improve the corrosion resistance of metal components. Metals like steel and aluminium can be prone to rust and corrosion when exposed to harsh environments. Applying a layer of a more resistant metal, such as nickel or zinc, creates a protective barrier that extends the lifespan of your components. For instance, nickel plating is particularly effective in providing robust protection against corrosion.
Improved Aesthetic Appeal
Electroplating can also enhance the visual appeal of metal parts. This is particularly important in industries where the appearance of a product is critical, such as consumer electronics and automotive manufacturing. Gold plating provides a luxurious finish, offering additional benefits like improved conductivity and resistance to tarnish.
Increased Electrical Conductivity
In the electronics industry, the electrical conductivity of components is crucial. Metals like gold, silver, and copper are excellent conductors, and electroplating these onto connectors, circuit boards, and other components can greatly improve their performance. Our copper plating services, for example, are widely used to enhance the conductivity and reliability of electrical components.
Wear and Tear Resistance
Components subject to high friction or mechanical wear benefit greatly from electroplating. Applying a hard-wearing metal layer to the substrate can significantly increase the durability of these parts, reducing maintenance costs and downtime. Our nickel plating services provide a hard, wear-resistant surface ideal for applications in the automotive and aerospace industries.
Reduced Friction
Electroplating can also reduce friction between moving parts, which is crucial in applications where components are subject to continuous motion and wear. Metals like silver offer excellent anti-galling properties, making them ideal for high-friction environments. This reduction in friction not only improves the efficiency of machinery but also extends the life of the components, reducing the need for frequent replacements and maintenance.
Versatility and Customisation
Electroplating is a highly versatile process that can be customised to meet specific requirements. Whether you need a bright, decorative finish or a functional coating with specific mechanical properties, Karas Plating can accommodate your needs. Our rack and barrel plating methods allow us to handle components of various sizes and shapes efficiently, ensuring consistent quality and performance across batches.
Thickness and dimensions
Electroplating enables precise control over material thickness. Unlike other processes that apply thick coatings, electroplating results in a thinner and more exact coating. This thin coating is crucial for components with strict dimension requirements.
Size of components
When it comes to metal finishing processes, size can often be a limiting factor. For instance, while hot dip galvanising can accommodate large components, smaller parts may present challenges. However, for a manufacturer specialising in producing small components, electroplating emerges as the superior choice. Electroplating is well-suited for small parts, decorative items, and components that demand precision.
More control
Electroplating is highly beneficial for components and substrates that need quality and consistent finish as it allows an even distribution of coating. Furthermore, if your components are uneven shapes and have hard-to-reach areas, the immersion factor of electroplating allows for quality, even finish on these more difficult parts.
Cost-effectiveness
Compared to other metal finishing processes such as powder coating, electroplating stands out as a more cost-effective method, allowing customers the benefit of plating large quantities of components at less cost than other methods.
A new lease of life to components
Electroplating is a technique for rejuvenating worn-out components, providing them with a renewed lifespan. This process offers a dual advantage by restoring lost performance due to wear and tear and enhancing the aesthetic appeal of products. Electroplating is particularly beneficial for components that have been in service for an extended period.
Metal preparation and cleaning
For the electroplating process to be successful, it is crucial to thoroughly clean and prepare the components before they can be plated. This cleaning and preparation step is essential for removing any contaminants that could otherwise impact the quality and durability of the plating. One of the main advantages of electroplating is the meticulous cleaning involved, which is incredibly valuable for ensuring the effectiveness and longevity of the plated surface, particularly for in-service and worn-out parts. That’s why we offer a range of blasting and cleaning processes that we use ourselves to prepare substrates for plating.
Sacrificial coating
Electroplating allows for sacrificial coating, which is a protective layer applied to a material, usually a metal, to prevent corrosion or wear. This coating is intended to deteriorate instead of the underlying material, thereby extending the life of the primary structure. With the right plating technique, your key components can be protected from rust, oxidation, and corrosion. Several methods will achieve this result, with zinc or a zinc/nickel alloy being among the most effective.
Wide range of materials
Whilst other industrial finishing methods like anodising cannot work with steel and other grades of aluminium, electroplating is more flexible and can be used to coat metals like stainless steel and carbon steel when we need to impart certain characteristics to components that are not present. For example, we often plate stainless steel with nickel to improve conductivity for computer components. Depending on the desired outcome, processes such as silver, gold, zinc, and nickel plating can be used.
ENHANCED CORROSION RESISTANCE
One of the primary benefits of electroplating is its ability to significantly improve the corrosion resistance of metal components. Metals like steel and aluminium can be prone to rust and corrosion when exposed to harsh environments. Applying a layer of a more resistant metal, such as nickel or zinc, creates a protective barrier that extends the lifespan of your components. For instance, nickel plating is particularly effective in providing robust protection against corrosion.
IMPROVED AESTHETIC APPEAL
Electroplating can also enhance the visual appeal of metal parts. This is particularly important in industries where the appearance of a product is critical, such as consumer electronics and automotive manufacturing. Gold plating provides a luxurious finish, offering additional benefits like improved conductivity and resistance to tarnish.
INCREASED ELECTRICAL CONDUCTIVITY
In the electronics industry, the electrical conductivity of components is crucial. Metals like gold, silver, and copper are excellent conductors, and electroplating these onto connectors, circuit boards, and other components can greatly improve their performance. Our copper plating services, for example, are widely used to enhance the conductivity and reliability of electrical components.
WEAR AND TEAR RESISTANCE
Components subject to high friction or mechanical wear benefit greatly from electroplating. Applying a hard-wearing metal layer to the substrate can significantly increase the durability of these parts, reducing maintenance costs and downtime. Our nickel plating services provide a hard, wear-resistant surface ideal for applications in the automotive and aerospace industries.
REDUCED FRICTION
Electroplating can also reduce friction between moving parts, which is crucial in applications where components are subject to continuous motion and wear. Metals like silver offer excellent anti-galling properties, making them ideal for high-friction environments. This reduction in friction not only improves the efficiency of machinery but also extends the life of the components, reducing the need for frequent replacements and maintenance.
VERSATILITY AND CUSTOMISATION
Electroplating is a highly versatile process that can be customised to meet specific requirements. Whether you need a bright, decorative finish or a functional coating with specific mechanical properties, Karas Plating can accommodate your needs. Our rack and barrel plating methods allow us to handle components of various sizes and shapes efficiently, ensuring consistent quality and performance across batches.
THICKNESS AND DIMENSIONS
Electroplating enables precise control over material thickness. Unlike other processes that apply thick coatings, electroplating results in a thinner and more exact coating. This thin coating is crucial for components with strict dimension requirements.
SIZE OF COMPONENTS
When it comes to metal finishing processes, size can often be a limiting factor. For instance, while hot dip galvanising can accommodate large components, smaller parts may present challenges. However, for a manufacturer specialising in producing small components, electroplating emerges as the superior choice. Electroplating is well-suited for small parts, decorative items, and components that demand precision.
MORE CONTROL
Electroplating is highly beneficial for components and substrates that need quality and consistent finish as it allows an even distribution of coating. Furthermore, if your components are uneven shapes and have hard-to-reach areas, the immersion factor of electroplating allows for quality, even finish on these more difficult parts.
COST-EFFECTIVENESS
Compared to other metal finishing processes such as powder coating, electroplating stands out as a more cost-effective method, allowing customers the benefit of plating large quantities of components at less cost than other methods.
A NEW LEASE OF LIFE TO COMPONENTS
Electroplating is a technique for rejuvenating worn-out components, providing them with a renewed lifespan. This process offers a dual advantage by restoring lost performance due to wear and tear and enhancing the aesthetic appeal of products. Electroplating is particularly beneficial for components that have been in service for an extended period.
METAL PREPARATION AND CLEANING
For the electroplating process to be successful, it is crucial to thoroughly clean and prepare the components before they can be plated. This cleaning and preparation step is essential for removing any contaminants that could otherwise impact the quality and durability of the plating. One of the main advantages of electroplating is the meticulous cleaning involved, which is incredibly valuable for ensuring the effectiveness and longevity of the plated surface, particularly for in-service and worn-out parts. That’s why we offer a range of blasting and cleaning processes that we use ourselves to prepare substrates for plating.
SACRIFICIAL COATING
Electroplating allows for sacrificial coating, which is a protective layer applied to a material, usually a metal, to prevent corrosion or wear. This coating is intended to deteriorate instead of the underlying material, thereby extending the life of the primary structure. With the right plating technique, your key components can be protected from rust, oxidation, and corrosion. Several methods will achieve this result, with zinc or a zinc/nickel alloy being among the most effective.
WIDE RANGE OF MATERIALS
Whilst other industrial finishing methods like anodising cannot work with steel and other grades of aluminium, electroplating is more flexible and can be used to coat metals like stainless steel and carbon steel when we need to impart certain characteristics to components that are not present. For example, we often plate stainless steel with nickel to improve conductivity for computer components. Depending on the desired outcome, processes such as silver, gold, zinc, and nickel plating can be used.
Different Electroplating Processes
At Karas Plating, we offer a wide range of electroplating processes, each designed to meet specific requirements:
Silver Plating
Ideal for enhancing conductivity and corrosion resistance, silver plating is widely used in the electronics, aerospace, and energy sectors.
Gold Plating
Offering excellent conductivity and resistance to tarnish, gold plating is perfect for high-reliability applications such as connectors and circuit boards.
Tin Plating
Known for its excellent solderability and corrosion resistance, tin plating is commonly used in the electronics and automotive industries.
Copper Plating
Copper plating offers superior conductivity and is often used as an undercoat to enhance the adhesion of subsequent layers.
Zinc Plating
Zinc plating provides outstanding corrosion resistance and is often used to protect steel components. This process is highly effective for applications in the automotive and construction industries.
Zinc-Nickel Plating
Providing exceptional corrosion resistance, zinc-nickel plating is ideal for components exposed to harsh environments, such as automotive and aerospace parts.
Flexibility
Electroplating offers flexibility not only in the variety of processes available but also in the methods used, making it suitable for a range of applications. At Karas Plating we have been using these methods for decades. By far the most popular are barrel plating and rack plating.
Small components at scale
Barrel plating involves loading small components into a barrel, which is then submerged into the plating solution. The barrel rotates on a central axis, allowing the components to tumble over one another and ensuring that all difficult-to-reach parts are evenly coated. This method is ideal for plating small parts at high volume, making it beneficial for mass production and quick lead times.
Large Components
On the other hand, rack plating is suitable for larger components, such as sheet metal and industrial machinery parts. Individual components are hung on a large rack, providing greater control over the plating process and allowing for precise thickness and coverage. Additionally, rack plating reduces the risk of damage to parts, making it a preferred method for plating larger items.
Applications Across Various Sectors
Electroplating finds extensive applications across multiple sectors. At Karas, we firmly believe that a wide range of industries in the UK benefit from electroplating. It’s hard to think of any industry in the UK that doesn’t benefit from electroplating in one form or another. Here are just a few examples:
Aerospace
Electroplating processes enhance the durability and performance of aerospace components. Silver, gold, and Iriditing are commonly used in aerospace applications.
A crucial example is the need for durability in components constantly exposed to extreme conditions, including temperature changes and heat, pushing them to their limits. Through electroplating and sacrificial coatings, an additional layer of protection is applied to these parts, ensuring they can withstand the demanding environment and prolong their service life. Iriditing is also key for this sector as it’s a chromate conversion coating. When applied to metals, like aluminium, it improves corrosion resistance and serves as a base for subsequent coatings.
This not only enhances durability but also contributes to safety and efficiency in aircraft, reduces the need for frequent replacements, ultimately cutting costs, and improving safety standards in the aviation industry.
Automotive
Electroplating is used for everything from the largest bodywork panels to the smallest electronic components and is a necessity at every stage of the vehicle manufacturing process. We employ a range of plating techniques that ensure the continuity of production that is so essential to running an effective car assembly line. Processes like zinc-nickel, silver and gold plating improve the corrosion resistance, conductivity and aesthetic appeal of vehicle parts.
With the development of electric vehicles, our plating techniques are as important as ever. Specifically, we provide nickel-plated busbars that act as the connector between the car and its battery. These copper or aluminium connectors require the additional strength and corrosion resistance that nickel delivers so well. Nickel is more resistant to heat, making it an excellent choice for electric vehicles as they generate substantial heat from the battery cells.
Electronics
The key role of electroplating in the electronics sector is improving the conductivity of connectors, contacts, and circuits. Electronic components gain enhanced conductivity and reliability with processes such as silver, gold, copper and tin plating.
Engineering
The field of engineering extensively relies on electroplating processes. At Karas Plating, a significant portion of our work involves plating and perfecting components for use in various engineering projects, emphasising the pivotal role of electroplating in this sector and discipline. Electroplating offers engineering numerous benefits, including uniformity across all parts, precision in metal finishing, the ability to scale plating for small components, and the achievement of high-quality finishes. Discover how engineering uniquely benefits from electroplating here.
Medical
The medical industry requires precise equipment constructed from high-quality electroplated components. Metals such as silver, gold, and copper are useful in the medical sector, particularly silver and gold, as they possess great natural resistance to bacteria. Additionally, the passivation of stainless steel is highly useful for medical instruments. It removes iron content from the surface of stainless steel, which helps to prevent surface rust and enhance corrosion resistance.
Energy
Energy applications need robust and reliable components. Conductivity, heat resistance and corrosion resistance are essential considerations. Silver, copper, gold, tin and zinc plating processes are widely used.
Rail
Rail infrastructure faces significant exposure to the elements, including prolonged exposure to wind, rain, and other harsh conditions. This exposure can lead to issues such as rust, water damage, salt corrosion, and general wear and tear. Plus, the nature of the operations means friction from interaction with other components, exposure to electricity and high speeds. To combat these challenges, the railway industry extensively uses electroplating methods to protect its components and enable this sector to stay on track and keep moving literally!
Electroplating is critical
In our experience, industries such as automotive, power generation, defence, petrochemical, and medical sectors all use electroplating to enhance production, boost reliability, and create sustainable products and components. This process is widely trusted for its speed, efficiency, quality, and long-lasting results across diverse applications.