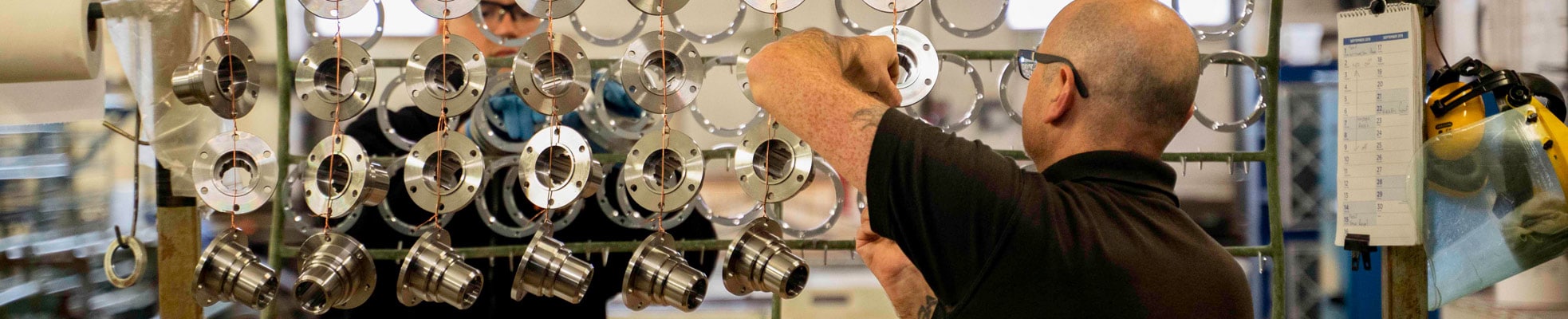
Think Zinc: the importance of zinc plating in combatting corrosion
As any of our regular customers will be aware, there are many types of electroplating processes available here at Karas Plating. Choosing the right method for your components depends entirely on the qualities you expect from them. Some metals offer greater conductivity, others better lubricity, and still others superior wear resistance.
If your main concern is to protect your metal substrate from corrosion, then zinc plating may be the right process for you. This cost-effective plating solution creates a reliable corrosion-resistant barrier when applied to ferrous metals, zinc is often referred to as sacrificial metal to protect ferrous materials, making it a popular choice over multiple industry sectors.
So how does it work?
A Protective Ring
Zinc plating provides a twofold method of rust protection. First, it forms a physical barrier across the substrate that protects the material from contact with moisture and air, preventing the oxidation process from taking place and rust forming on the core metal. Since zinc itself is naturally resistant to rust, it corrodes at a much slower rate.
A Sacrificial Coating
Not only is zinc corrosion-resistant in its own right, when bonded to a steel substrate, that steel will not corrode as quickly. This is even true if the zinc coating has been cut or punctured, exposing the steel core. Even under these circumstances, the zinc coating corrodes first. With other coating techniques, such as paints or aluminium, once the coating has been breached, the substrate is immediately susceptible to rust.
Additional Benefits
While protection against corrosion is a common reason to go for zinc plating, the metal processes have other qualities worth your consideration. Zinc is an abundant metal, making it a cost-effective choice for many customers. It is possible to apply a range of different finishes to zinc plating, from a bright gleam to textured surfaces. Zinc also boasts impressive adhesive qualities, making it an ideal primer layer for painted components.
Testing for Corrosion Resistance
To determine the protective qualities of the zinc plating process, sample parts are put under exaggerated atmospheric conditions (salt spray) which is exactly what it sounds like. Sample components are subject to a constant spray of salt and water until first signs of corrosion (white rust) with the time in hours recorded the process will then continue until the 2nd signs of corrosion (red rust) again with time recorded in hours. As corrosion is measured in hours the corrosion resistance time can differ with thicker deposits of zinc, passivations and rack or barrel plating process with times varying from as little as 8 hours to 720 hours.