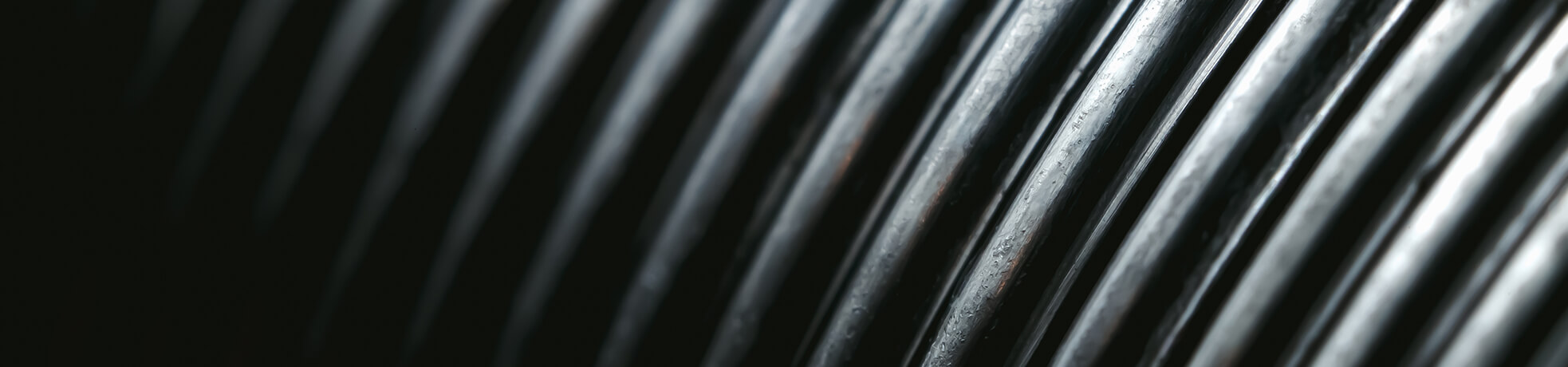
Zinc phosphating (also know as zinc phosphate conversion coating) is used in dozens of industries for hundreds of applications. It is a way to chemically treat steel and galvanised steel substrates (as well as some other materials) which results in a thin layer of zinc adhering to the base metal. In this article, we’re going to look at just a handful of the ways zinc phosphating is used and some of the properties it confers to the substrate.
Applying zinc phosphate
Zinc phosphate conversion is performed by applying a dilute solution of phosphoric acid and soluble zinc directly to the steel substrate. This is usually applied via immersion in a bath of solution or by spraying that solution onto the steel. This causes a reaction, raises the pH level of the solution and causes the zinc phosphates to form a bonded deposit over the substrate.
Beneficial properties of zinc phosphate conversion coating
Why apply zinc phosphating to your substrate in the first place? Well, it has several qualities that make it attractive to a wide range of industries. These include:
Adhesion
Zinc phosphate has great adhesive qualities, often being used as a primer for further coatings or paints.
Corrosion resistance
Zinc phosphate is an excellent method of corrosion resistance, being lighter than other forms of protective plating. Since it can be applied via immersion or using a spray, it can be used with large and small components alike.
Wear
resistance
Zinc phosphate is used to coat components that are subject to wear, creating an even, protective barrier.
Lubricity
When treated with sodium stearate (soap), zinc phosphate becomes an effective lubricating layer on metal substrates. The phosphate crystals react with the soap to form an insoluble and hydrophobic barrier on the surface of the metal.
Applications of zinc phosphate conversion coating
Thanks to its beneficial qualities mentioned above, zinc phosphate offers some incredible advantages. These are some of its most common applications across various industries:
Automotive industry
Almost all commercial cars have a zinc phosphate conversion coating to protect the bodywork from corrosion and provide an adhesive primer layer for painting.
Engineering
Since many engineering projects involve moving parts, the lubricity and wear resistance offered by zinc phosphating is of huge importance.
Anti-galling treatment
Galling refers to a specific type of wear between sliding surfaces. If the two surfaces are being compressed with sufficient force, some of the material from surface A can be pulled along by surface B, warped it out of shape. This commonly occurs with threaded or geared components and can cause serious damage to major engineering works. A zinc phosphate conversion coating not only protects the metal components from wear one, but also lubricates the surface for freer movement.