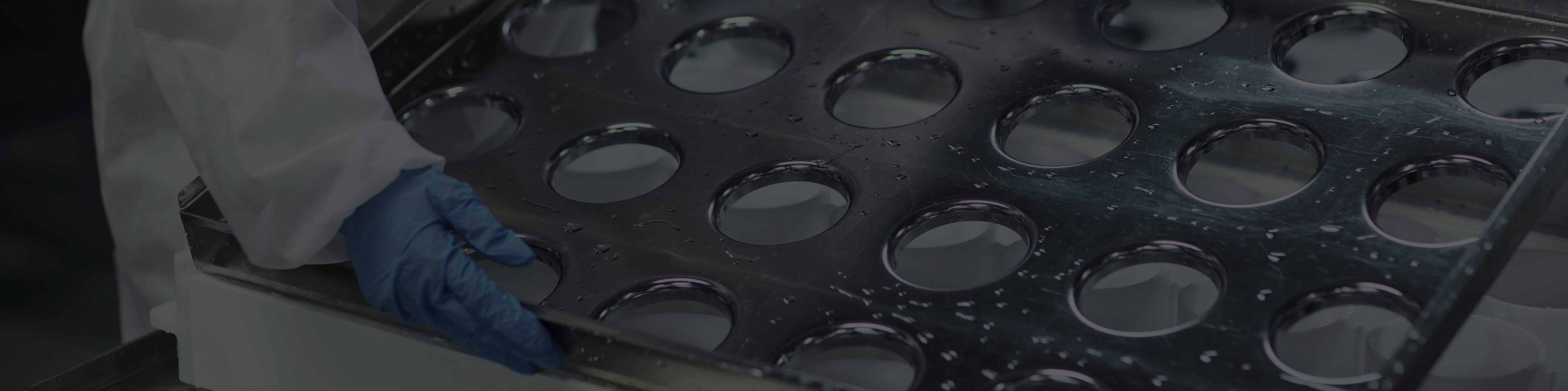
Tin plating is a widely used electroplating method that enhances the durability and corrosion resistance of metal surfaces. This guide explores the key properties of tin, details the tin plating process, and highlights the unique advantages of both bright and dull tin plating. We’ll also cover sourcing practices and environmental compliance, providing a comprehensive resource for understanding the benefits of tin plating across various industries.
What is Tin? Key Facts About the Metal
Tin has been utilised for millennia and continues to play a critical role in modern industries. Known for its versatility and non-toxic nature, tin is highly valued for its corrosion resistance, ductility, and ability to resist tarnishing. It is also recognised for its suitability in soldering and for providing protective coatings in a wide range of applications.
Chemical Symbol: Sn (derived from the Latin Stannum)
Melting Point: 232°C (450°F), making tin suitable for low-temperature applications.
History: Tin has been used since ancient times, with its earliest use dating back to 3,500 BC in alloys like bronze.
Properties of Tin
Tin is malleable – meaning that it can be pressed, beaten or hammered into a different shape without breaking or cracking, for example, into sheets. Tin is ideal for plating components where good surface adhesion is needed for a good protective barrier. The malleability of tin is vital in this as it can be easily formed and shaped onto the component’s structure without cracking or breaking, providing great protection.
The Tin Plating Process Explained
Tin plating typically involves depositing a layer of tin onto a metal surface to enhance its durability and performance. The process can be tailored to achieve bright tin plating or dull tin plating, depending on the desired finish.
Surface Preparation
This critical step removes all contaminants (such as oil, dust, or oxidation) that may affect plating quality. Methods include degreasing, pickling, and acid etching to ensure a clean substrate for effective tin adhesion.
Electroplating
The prepared substrate is immersed in a tin ion solution, and an electric current is applied. This causes tin ions to deposit onto the metal surface, forming a uniform coating. The process can result in:
Bright Tin Plating: Produces a reflective, shiny surface ideal for decorative or high-conductivity purposes.
Dull Tin Plating: Yields a matte finish that offers reduced friction and enhanced solderability, suitable for applications requiring a non-reflective surface.
Post-plating Treatment
Post-treatment processes such as passivation or baking are employed to further enhance the durability of the tin plating and mitigate issues like tin whiskering, which is common in electronic applications.
Types of tin plating
When it comes to tin plating components, choosing between barrel plating and rack plating requires careful consideration.
Barrel plating
Barrel plating tin components is suitable for bulk quantities of small items, as they are placed in a rotating barrel and immersed in a chemical bath. This method is cost-effective but may not be ideal for larger components.
Rack Plating
On the other hand, rack plating is more suitable for larger tin components. They are placed and hung onto a large rack attached with hooks. The separation between the components makes rack plating great for tin plating applications where precision is vital.
Which method is best for tin plating components
When it comes to choosing the optimal tin plating method for your parts, it’s essential to understand that size is just one of several factors to consider. At Karas Plating, we advise evaluating each case individually, considering factors such as the component, shape, type, contact surface, and the fragility of the components. If you’re uncertain about the best approach for your specific needs, don’t hesitate to get in touch with us. We’re here to provide the assistance you need. Bright Tin Plating and Dull Tin Plating serve distinct purposes and are tailored to meet specific industry requirements. Here’s how they compare:
Bright Tin Plating
Bright tin plating is achieved by incorporating specific additives in the electrolyte bath, resulting in a highly reflective and lustrous finish. This type of tin plating is often chosen for:
Aesthetic Purposes: The shiny, polished surface is visually appealing, making it popular for decorative components.
Enhanced Conductivity: Bright tin is frequently used in electrical and electronic components due to its superior conductivity and low contact resistance.
Wear Resistance: The bright finish offers a slightly harder surface compared to dull tin plating, beneficial in environments with minimal friction.
Applications
- Electrical connectors and terminals
- Decorative parts in consumer electronics
- Automotive components requiring an attractive finish
Dull Tin Plating
In contrast, dull tin plating provides a matte, non-reflective appearance and is often applied where aesthetics are secondary to functionality. Dull tin offers:
Superior Solderability: The matte finish allows for better soldering, making it ideal for electronic components that require precise solder joints.
Lower Friction: The less glossy surface reduces friction, which is important in certain moving mechanical parts.
Non-reflective Surface: Preferred in sectors where light reflection could cause interference or is unnecessary.
Applications
- Circuit boards and electrical components
- Aerospace and automotive connectors
- Food-safe applications where a reflective surface is unnecessary
Sourcing and Materials Policy: Responsible Tin Supply
At Karas Plating, we ensure that all of our tin is sourced from suppliers who meet stringent environmental and ethical standards. We operate under an Environmental Permit, which guarantees that our processes adhere to strict environmental regulations. Our commitment to compliance with REACH and RoHS ensures that harmful chemicals are avoided, and our plating services meet the latest safety and environmental standards.
REACH Compliance: We adhere to the European Union’s REACH regulation, ensuring that all chemicals used in our plating processes are evaluated for their safety and environmental impact.
RoHS Compliance: RoHS restricts the use of hazardous substances in electrical and electronic equipment. Our tin plating services comply with RoHS directives, meaning that the materials we use are free from harmful substances like lead, mercury, and Cadmium.
More on our REACH and RoHS compliance
Our Environmental Permit further demonstrates our commitment to reducing environmental impact while maintaining the highest quality standards in all of our plating services.
PROS AND CONS OF TIN PLATING
PROS
Corrosion Protection: Tins resistance to oxidation prevents corrosion, particularly in humid or chemically active environments.
Solderability: Tin offers excellent solderability, especially in dull tin plating applications, ensuring strong and reliable solder joints.
Ductility: Tins highly ductile nature allows it to be bent and manipulated without weakening, enhancing its versatility in complex applications.
Cost-efficient: Tin is less expensive than precious metals like silver or gold, yet still provides significant protection and performance.
Food-safe: Tin is non-toxic and widely used in food-related applications like packaging and machinery.
Non-magnetic: Tin plating does not interfere with magnetic properties, making it a suitable choice for electrical components.
CONS
Whiskering: Tin plating, particularly bright tin, can produce whiskers—small, sharp protrusions on the surface that are invisible to the naked eye. These microscopic fibres are highly conductive and can cause shorts in electronic devices. While there’s no guaranteed solution to eliminate whiskering, the use of dull tin plating reduces the risk, thanks to its larger tin grains.
Perishable Solderability: Although tin offers excellent solderability, this property can diminish over time. The solderability of the tin-plated surface can degrade, especially if the substrate is not properly prepared. However, at Karas Plating, we take special care in preparing the substrate to ensure long-lasting solderability and maintain the quality of the tin coating.
Sectors That Benefit from Tin Plating
Tin plating is employed across a variety of industries due to its versatility and numerous benefits. Here’s a closer look at sectors that frequently rely on either bright or dull tin plating:
Electronics
Tin plating is indispensable in the electronics industry due to its excellent electrical conductivity, solderability, and corrosion resistance. Whether for circuit boards, connectors, or terminals, both bright and dull tin plating provide essential protection and functionality.
Automotive
The automotive industry uses tin plating to protect connectors, fasteners, and terminals from corrosion, particularly in high-moisture or chemically aggressive environments. Tins cost-effectiveness and performance make it an ideal choice for under-hood components and electrical systems.
Aerospace
Aerospace components are often exposed to extreme environments. Dull tin plating is particularly beneficial for parts that require both corrosion resistance and solderability in electrical systems, while bright tin may be used where reflectivity and conductivity are key.
Food Processing
Tin is widely used in the food and beverage industry due to its non-toxic, corrosion-resistant properties. Tin-plated surfaces help protect food from contamination, making it an essential material for containers, processing equipment, and packaging.
Why Choose Karas Plating for Tin Plating?
At Karas Plating, we offer a comprehensive range of tin plating solutions to meet the unique demands of our clients. Whether you’re looking for bright tin plating for its aesthetic appeal and conductivity or dull tin plating for its superior solderability and reduced glare, our team delivers consistent, high-quality results.
Our Expertise
With over 70 years of experience, we’ve honed our expertise in electroplating. Our state-of-the-art facilities allow us to apply precise, durable tin coatings tailored to your needs. From small prototype runs to large-scale production, we provide quality service at every stage of the plating process.
Commitment to Sustainability
Karas Plating is committed to minimising our environmental impact. We operate under an Environmental Permit and ensure compliance with REACH and RoHS to provide responsible and high-quality plating solutions. Our dedication to sustainability aligns with our commitment to offering industry-leading tin plating services.