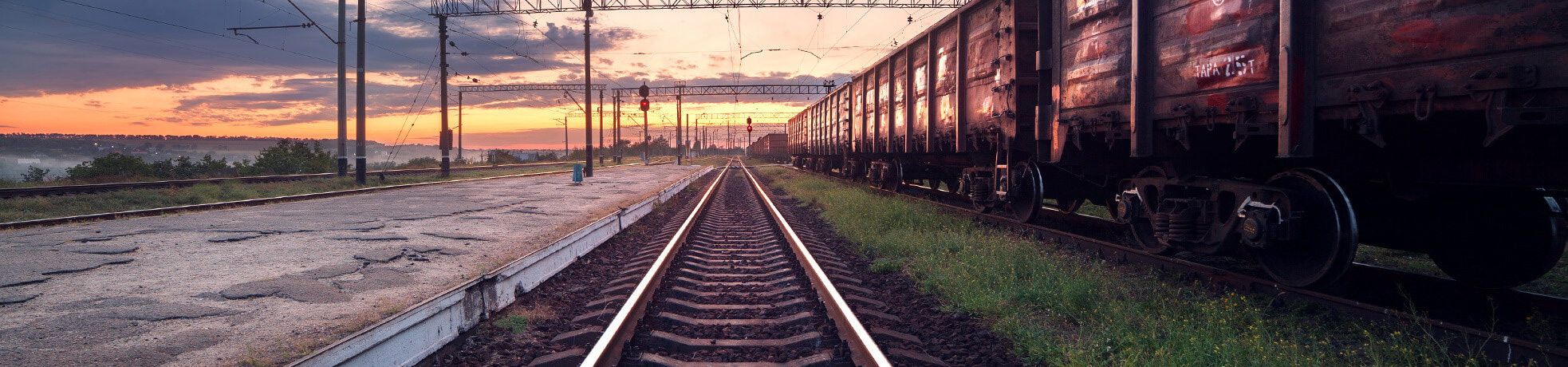
Like many industries across the UK, the British rail network depends on electroplating techniques on a day-to-day basis.
From the rails that carry passengers and freight across the country, to the engines and carriages that travel along them, to the precision electronics used to control the system, electroplating methods are in constant use across the rail network.
But why are these plating processes so important? What purpose do they serve in protecting our national rail infrastructure?
Exposure
Both trains and railway lines are exposed to the elements for prolonged periods of time. While some engines and carriages might be stored undercover, most of the countries rolling stock is left outside to face the wind, rain, and other inclement conditions.
This makes them susceptible to rust. A simple way to protect vital components is to use a corrosion-resistant plating method, such as zinc-nickel plating to form a protective barrier.
Wear and tear
Trains are built to last, with the average lifespan of a new model being around 30-35 years. To achieve this, they need protection against the day-to-day wear they are exposed too.
High speeds, sudden changes in temperature, and regularly stopping and starting can all result in serious deterioration of train components. A strong and durable plating technique, such as electroless nickel plating can help stave off this wear and tear.
Friction
Modern trains are a miracle of precision engineering, with thousands of individual parts moving against and alongside each other in perfect motion. Of course, as any engineer knows, this causes large amounts of friction, which can lead to overheating of key components.
A coating of zinc-nickel can help alleviate this problem, reducing friction and hardening the substrate simultaneously. Other treatments, such as zinc phosphate coating, can help increase lubricity for a smoother motion.
Conductivity
Of course, it’s not just the engines, the rails, and the rolling stock that need the assistance of quality electroplating. The trains’ control systems (and those of the rail network itself) need both speed and accuracy to keep the rail system running safely.
This requires highly-conductive plating techniques to ensure the electronics in those controls are up to the job. Gold is a popular choice for these applications, though silver plating is often preferred for large scale projects, as it is more cost-effective, with a comparable conductivity rate.