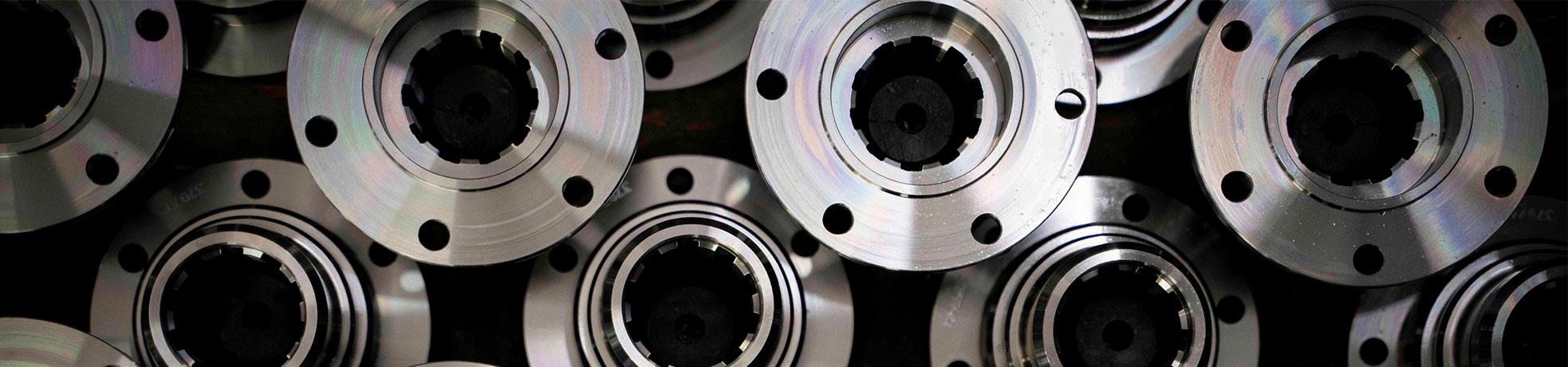
As the premier metal finishing firm in the North West, we know a thing or two about metal corrosion here at Karas Plating.
It is one of the most destructive phenomena to affect all sectors of British industry from automotive and telecommunications through to cars, oil and gas, and many more.
Fortunately, there are things any company can do to mitigate – if not completely eradicate – metal corrosion.
What is metal corrosion?
Corrosion is the gradual deterioration of a material cause by a chemical reaction to their environment. Specifically, metal corrosion describes the process of refined metal being transformed into a more chemically-stable form. These include oxides, hydroxides, and sulphides.
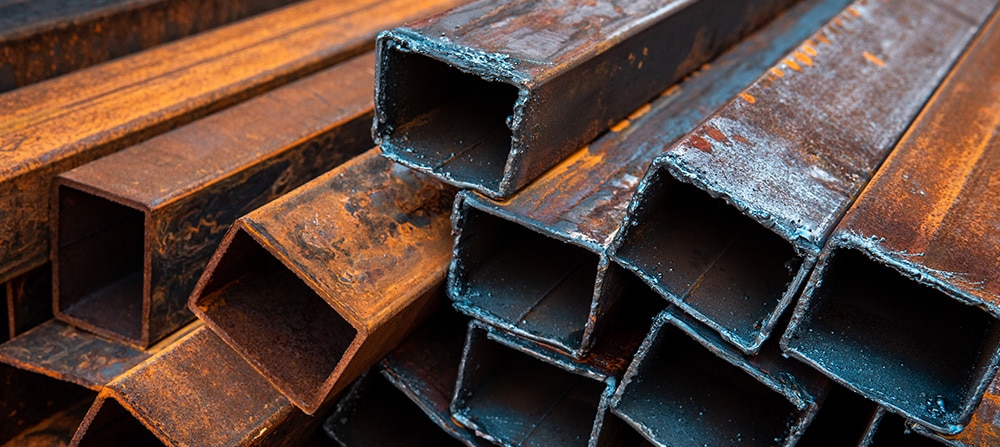
What causes metal corrosion?
There are various external elements that can contribute to metal corrosion. The most common are moisture and salt, both of which cause serious damage to unprotected steel surfaces. Both are highly-conductive and act as an electrolyte, allowing the spread of rust across your metal. Likewise, things like soil and clay can also cause corrosion, as can certain acids and alkaline found in the smoke and fumes from some industrial processes.
What can be done to prevent metal corrosion?
There are several ways to slow down metal corrosion. Here are some of the more common ones:
1.
Impressed current
Rust is spread by a current running between any existing corrosion and the fresh iron or steel. It is possible – with the right equipment – to produce a current of equal strength, flowing in the opposite direction. It’s a delicate task, requiring a lot of careful engineering and planning to get it just right. As such, it tends to be used in underwater projects such as pipes and buried tanks, where water, soil, and other electrolytes cannot be avoided.
2.
Primers
Primers and other coatings form a barrier between the elements and the base steel. This prevents the surface of the steel components from encountering corrosive elements in their surroundings.
3.
Plating
Our speciality! Like primers, metal plating acts as a shield for your iron or steel substrate. A different, more resistant metal is bonded to the surface of your steel, acting as a shield against those destructive environmental factors.
Often these are sacrificial metals – that is, a metal that reacts to the environment before the core metal. As this surface metal deteriorates, it releases its electrons into the substrate, protecting it against the elements. No metal remains rust-free forever. Plating will certainly help to slow the process, though further applications may be required over time.