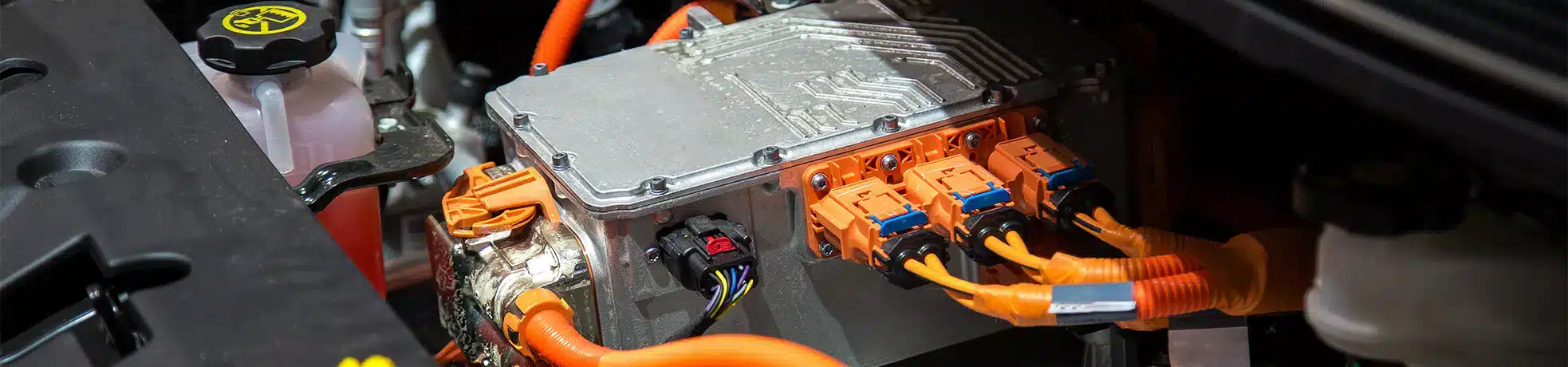
In the evolving landscape of the automotive industry, the UK government has set forward-looking targets to reduce vehicular emissions. By the recently updated target date of 2035, the sale of new internal combustion engine cars and vans will be banned, and consumers will be forced to purchase vehicles that don’t emit carbon out of their tailpipe. As a result, there has been a significant shift towards electric vehicles (EVs) that are expected to represent an ever-increasing percentage of vehicles on our roads.
Of course, with a larger proportion of electric vehicles on the market, the reliance on busbars will be greater than ever. Car manufacturers, eager to demonstrate that their EVs are as efficient as their fossil fuel vehicles, will need reliable and effective busbars with which to power them. In this article, we’re going to talk about the importance of busbars to the electric vehicle industry and how quality busbar plating is essential to their success.
What are busbars?
Busbars are solid bars of metal (typically copper or aluminium) that are used as conducting rods to connect points in a high-power electrical transfer or distribution circuit. These connectors help all manner of electrical appliances operate at optimal efficiency.
What are busbars used for in electric vehicles?
Almost everything. Since an electric vehicle is essentially a collection of discrete circuits and batteries, busbars play a crucial role in getting the whole thing working together. They connect the battery, the onboard computer, and all key components to one another in an elaborate network that relies on precision engineering and quality materials to deliver the results expected of it.
What materials are busbars made of?
Busbars are normally made of aluminium or copper, both of which have their particular benefits depending on the specific applications. Both offer high levels of electric conductivity, which explains their importance in the industry.
Copper
Copper offers greater conductivity than aluminium, making it a popular choice for busbars connecting high-performance circuits.
Aluminium
Aluminium, on the other hand, is lighter, cheaper, easier to work with, and generally more versatile than copper, not to mention being easier to recycle.
CCA
Another type of busbar is the copper clad aluminium busbar (also known as CCA busbars or bimetal conductive busbars). As the name suggests these products comprise an aluminium core wrapped in a layer of copper, giving the busbar the beneficial qualities of both metals.
Why is busbar plating so important in the electric vehicle industry?
While copper and aluminium have many valuable properties for busbar production, the application of a layer of nickel plating adds some additional qualities that are crucial for improved vehicle performance. These include:
solderability
This makes electroless nickel suitable for traditional welding as well as ultrasonic welding methods.
corrosion resistance
Electroless nickel plating offers enhanced corrosion resistance, which can be further enhanced by adding a thicker layer.
adhesion
Electroless nickel adheres extremely well to aluminium substrates, common in busbar production.
uniformity
Electroless nickel is deposited at a uniform rate, making it ideal for mass application across many individual busbars.
deposition
Trained electroplating engineers can calibrate the desposition of electroless nickel with extreme accuracy, depending on the needs of the client.