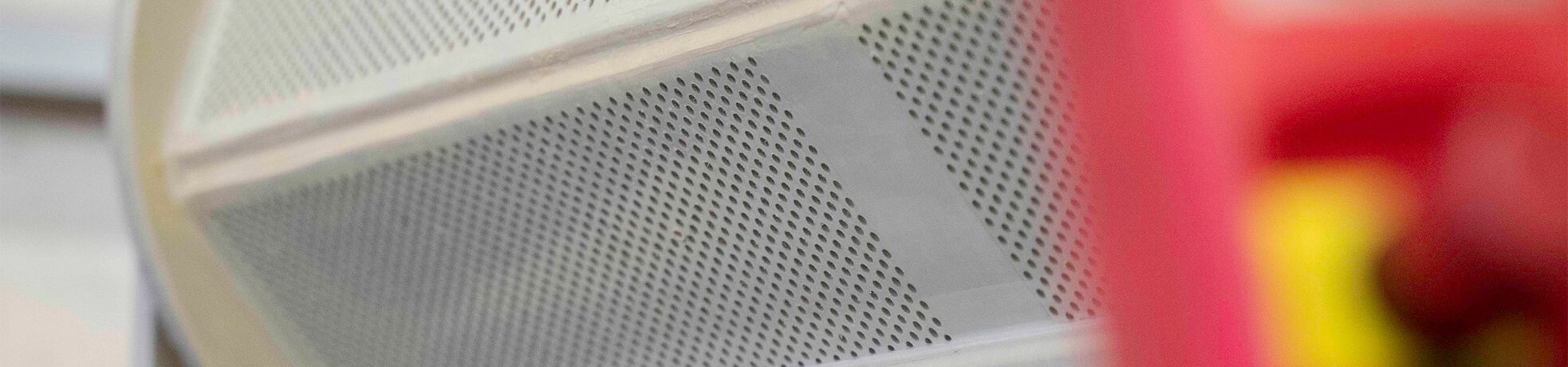
Electroplating is an effective way of coating a particular surface (or substrate) with a layer of metal. While the materials and the techniques might differ slightly, they all involve submerging the substrate into a metal containing solution and applying an electrical charge to trigger the plating process. There are a couple of ways to go about submerging your base materials in the solution, of which the most popular are rack plating and barrel plating.
In this article, we will explain what both of those methods are, when they are likely to be used, and explore the advantages and disadvantages of each.
Rack Plating
Rack plating is a straightforward method of plating larger or more delicate components that are too big for the barrel plating process. As the name implies, the substrate is fitted onto a wire rack and completely submerged in the vat of plating solution. The substrate remains stationary throughout the plating process, allowing for an even coating of metal even on complicated parts.
Advantages of Rack Plating
Perfect for larger components
Can get a thicker coating of metal on the substrate
Lack of motion means delicate components are better protected
Better for intricate and contoured surfaces
Disadvantages of Rack Plating
More labour intensive than barrel plating
More costly than barrel plating
May require the design and construction of a bespoke rack
Barrel Plating
Barrel plating is most commonly used for plating large numbers of smaller components, such as stampings and fasteners, in one process. The parts are loaded into a perforated barrel, which is then lowered into the plating solution. While the current is applied directly to the substrate in rack plating, with hundreds or thousands of components in the barrel, that simply isn’t feasible. Instead, the barrel has a metal core through which the electrical charge is applied. The barrel turns in the solution, which sees the individual parts tumbling and cascading over one another, ensuring a uniform distribution of the plating solution across all components.
Advantages of Barrel Plating
A cost-effective way of plating many small parts at once
Can be used to plate different sizes and shapes of components simultaneously
Less labour intensive than rack plating
Disadvantages of Barrel Plating
Can take longer to coat components, as it uses a lower electrical charge
Not suitable for delicate components
Which is the right process for me?
It entirely depends on your specific plating requirements. While the information in this article should give you some idea of which approach will work best for your plating project, we appreciate that it might not always be crystal clear. If you have any questions about either process, feel free to give us a call. One of our experienced and friendly plating experts will be happy to help.