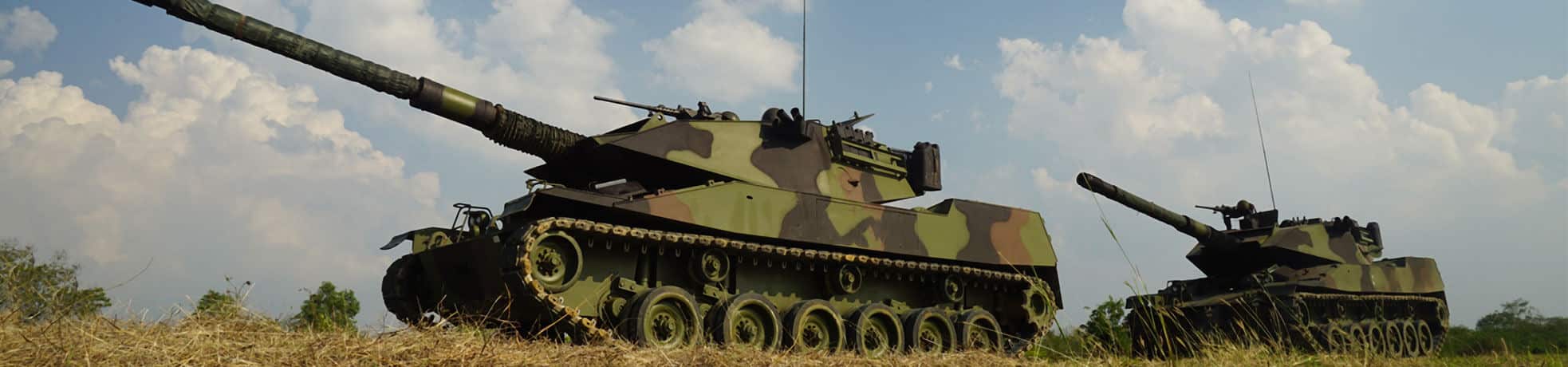
Electroplating and metal finishing have thousands of applications across hundreds of industry sectors. Each of these sectors demands a high standard of plating to ensure that their components are of the highest quality and can be relied upon to do the job that they were designed for.
The military sector is no exception. When plating components for any section of the Armed Forces, care and attention to detail are of the utmost importance. The quality of plated components for any kind of military application could literally be a matter of life or death. Heavy-duty vehicles and equipment, such as the Challenger 11 tank and other front-line machines require reliable place components of the highest quality.
Copper plating has many applications in the military, being a highly versatile material that can be plated to most metal substrates. It’s highly conductive and offers excellent adhesive qualities. This makes it a good choice as a sandwich layer between the existing substrate and a further application of metal plating. Because it is relatively cheap, copper is also a cost-effective solution to act as a primer. Its adhesive qualities make it the perfect surface for applying paints and glues, while also benefiting from its corrosive-resistant qualities.
Both manganese phosphate and zinc phosphate are used extensively in the military. These metal-finishing processes apply a thin and even film to even the smallest components, imparting several benefits to the metal parts. Manganese phosphate is highly durable and resistant to friction, making it a reliable finish for any device involving moving parts. Zinc phosphate offers great adhesion to components and is often applied as a primer for waxes, oils, and lubricants. Both phosphates are extremely lightweight, which is a key consideration when coating parts intended for military aircraft.
Zinc plating is chiefly employed for its corrosion-resistant qualities. Few other metals provide as much protection against rust as zinc does. This is a major concern for military applications, as vehicles and equipment are often deployed to the most inhospitable environments. Zinc is often applied as a sacrificial coating, whereby the harshness of the surroundings will need to eat through the zinc before reaching the more delicate and/or expensive metal of the substrate.
Zinc is often mixed with nickel, adding further beneficial qualities. The addition of nickel to the alloy provides great protection at high temperatures, which is important in military machinery and vehicles.