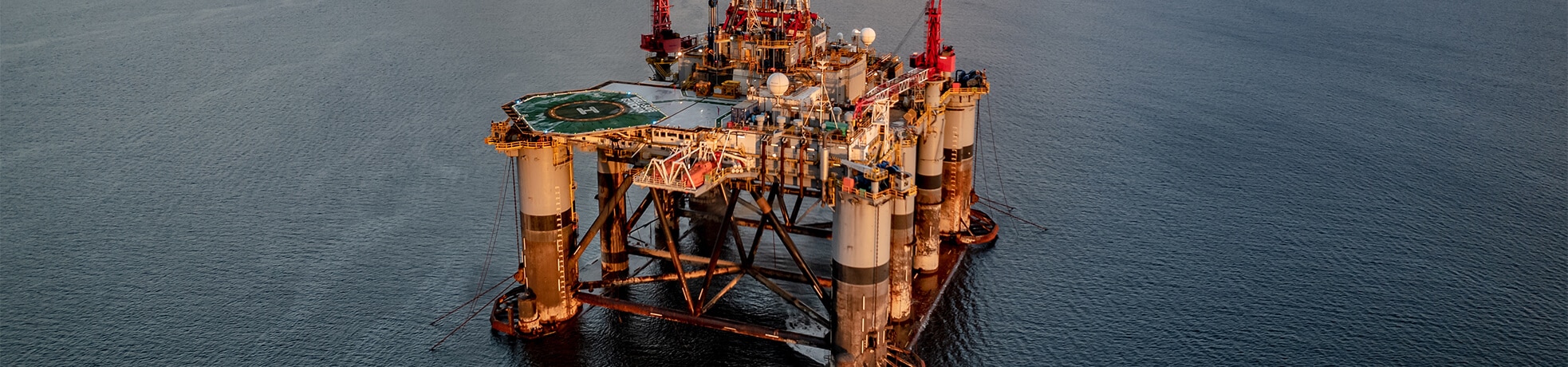
The oil and gas industry (not to be confused with the petrochemical industry – although they are closely linked) is one of the country’s most important sectors. Primarily concerned with locating and extracting natural gas and crude oil, the industry is also responsible for transporting those crucial raw materials to refineries. This is where they are filtered and processed into essential products such as petroleum, plastics, and detergents.
Each stage of oil and gas production and distribution requires durable components that can withstand the harshest of working environments. For this reason, thousands of companies within the industry depend on durable and reliable electroplating solutions to ensure all constituent parts are fit for purpose.
In this article, we look at some of the ways in which electroplating can assist the oil and gas industry.
Copper is one of the most important electroplating methods used by the oil and gas industry. Quite aside from boasting high-levels of resistance to heat and corrosion, it has another essential quality – prevention of marine growth. With so much oil and gas extraction taking place at sea, everything from the rigs to the network of distribution pipes is affected by seawater and the hundreds of micro-organisms that inhabit it. Algae, limpets, lichen, and barnacles are just some of the tiny creatures and plants that set up home on any static surface, slowly corroding the metal underneath.
Copper is not conducive to sea life, and they have a tough time colonising a copper surface, which is why this method is so crucial to the industry as a whole.
Oil and gas extraction involves heavy-duty machinery, incorporating hundreds of moving parts, both large and small. The constant movement of these parts against one another produces high levels of friction, resulting in increased temperatures and abrasion damage. While a coating of nickel (see below) can reduce the impact a little, the application of a phosphate coating can improve lubricity, which reduces friction at the source.
Electroless Nickel Plating (or ENP) is another popular metal finishing technique used in the oil and gas industry. Not only can it be applied evenly across the substrate, ensuring total coverage (essential for components that will be regularly submerged in seawater), but it acts as a sacrificial layer for the metal beneath. This protects your components from corrosion, wear, abrasion, and heat damage.
Plating in the oil and gas industry is used for more than just rigs, well-heads, and other heavy-duty machinery. Locating and extracting oil and gas requires instruments that incorporate delicate electronics. Gold plating is a popular choice for such components, as it delivers incredible conductivity – absolutely essential for the precise measurements and accurate performance demanded by the sector.