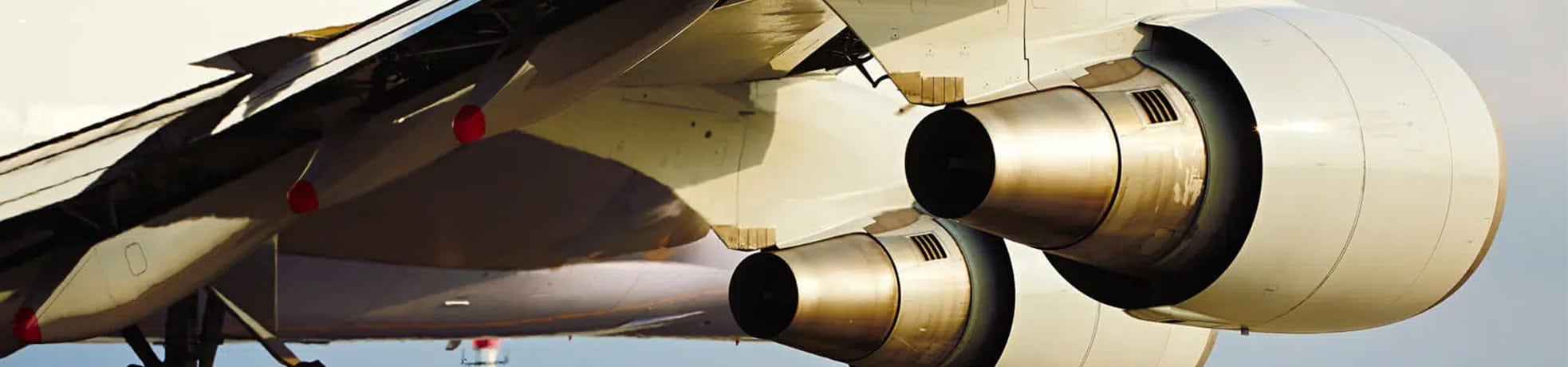
The British aerospace industry is a multi-billion pound concern. While people tend to think of it in terms of commercial aircraft, it actually encompasses a wide range of sectors, including unmanned aircraft systems, aviation security, airport infrastructure, alternative aviation fuels, rotorcraft, and so much more.
Each of these sectors requires electroplated components in some form or another, in order to function smoothly. Because of the materials used in the aerospace industry and the harsh conditions they undergo every day, all aerospace plating must be of the highest possible standard.
Plating onto Aluminium
Aluminium is one of the most common materials used in construction of commercial, military, and private aircraft, as well as unmanned vehicles and drones. It is lightweight and durable, whilst also being easy to machine and cast, making it perfect for aerospace projects. Aluminium is also non-corrosive, non-magnetic, and non-sparking, as well as being a good conductor for both heat and electricity. All these properties make it the ideal material for many applications in the industry.

Plating onto Steel
Steel is another popular metal used in aircraft construction. It is a strong metal, often used for frameworks, and can be easily plated to impart additional properties that are beneficial to the industry. A common form of plating for this purpose is copper plating. Copper provides good protection against corrosion and heat while retaining the solid steel core of the substrate. In addition, copper acts as an effective layer for further plating processes.
Electroless Nickel Plating (or ENP) is a method of coating an aluminium substrate through a chemical reaction. It delivers a more even, uniform coating across the whole of the component, making it an excellent choice for aircraft, where a full coating is essential for safety and performance. The nickel acts as a sacrificial layer, protecting the aluminium core from corrosion, wear, and abrasion.