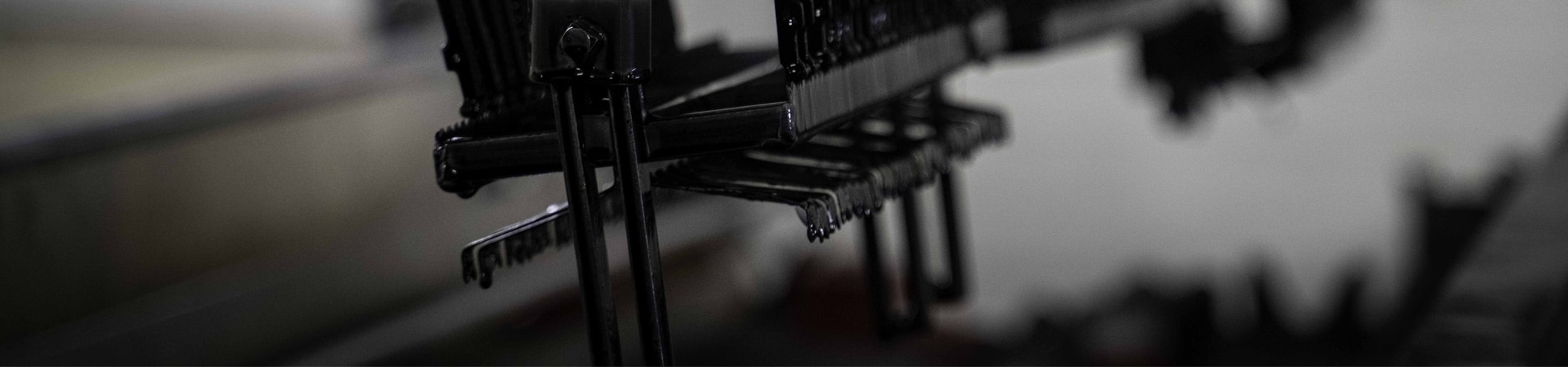
Hidden extras: the many applications of manganese phosphate coating
Here at Karas Plating, we work with an extensive range of metals as part of our plating processes – each of which has its own unique qualities that make it perfect for the job in hand. Many of our customers understand the properties and advantages of the more familiar metals – gold, silver, and tin, for instance – while others are a bit more of a mystery.
Manganese, for instance, probably wouldn’t appear on anybody’s top ten list of recognisable metals, yet it is one of the most useful elements for a whole host of reasons. It is essential to the steel industry, where it is used to remove phosphorus, oxygen, sulphur, and other contaminates. These very properties are what makes it so useful in the plating sector too, usually applied as a manganese phosphate coating.
manganese phosphate coating?
Manganese phosphate coating offers many beneficial properties. When applied to a steel surface, it creates a crystalline finish that absorbs oil and other lubricants. It offers excellent corrosion resistance to many metals and its hardness and resistance to wear and tear provide a high standard of protection. It also has good adhesive qualities, making it a fine choice for pre-treating metal surfaces prior to painting or coating.
What Is Manganese Phosphate Coating Used For?
Manganese phosphate coating has many applications, as it noticeably reduces incidences of corrosion, wear and tear, and galling. Its anti-corrosion properties mean manganese phosphate coating is regularly used in the automotive trade for nuts and bolts, brakes, washers, and magnet cores among others. It has effective lubrication qualities, making it a popular choice for projects that involve moving parts sliding against one another. Naturally, it is much in demand in the manufacture of engines, power transmission systems, gears, and more.
What Is the Manganese Phosphate Coating Process?
Manganese phosphate coating is a long and involved process, requiring several distinct phases. These include degreasing and cleaning of the substrate, followed by a water rinse and an acid wash. Then it undergoes a further water rinse, activation, and the manganese phosphate coating itself. After one final water rinse, the components are lubricated using special oils.