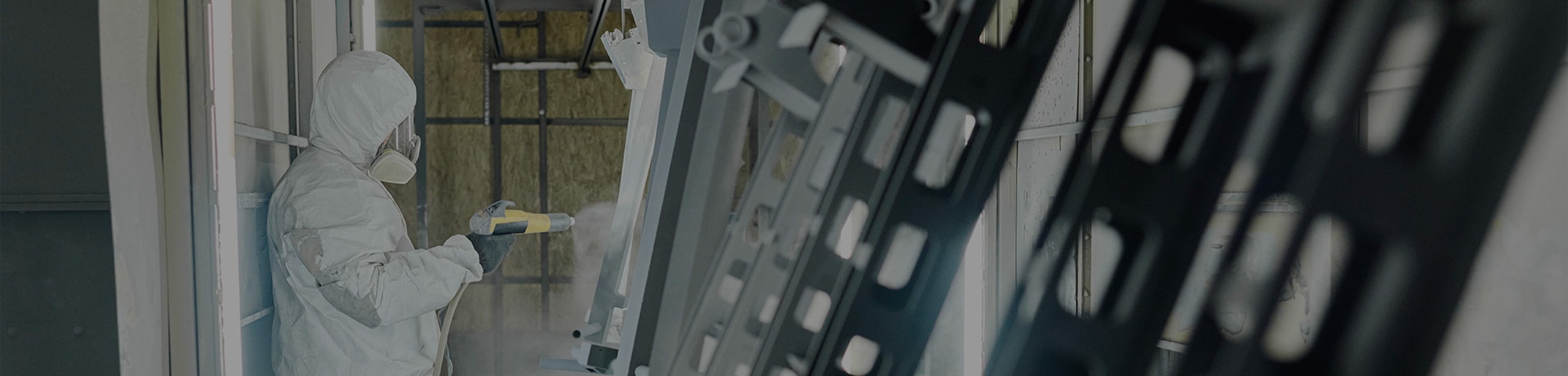
What is busbar surface treatment?
Busbar surface treatment is the process of applying a protective coating or layer to the surface of a busbar to improve its performance, durability, corrosion resistance, and safety. One of the most common surface treatments is plating, where a thin layer of metal is applied to enhance properties like strength and electrical conductivity. Common plating processes for busbars include silver plating, tin plating, and nickel plating.
The role of busbars
Busbars play a vital role in critical applications, and various methods are employed to enhance their performance. This ensures reliability and availability across a diverse range of uses, from power distribution to energy, automotive, aerospace, and marine applications. Continuous innovation in this field enables the creation of high-quality busbar components, driving progress and excellence in engineering.
One of the most popular ways to improve busbar performance is through powder coating or electroplating. These two methods have a long history and offer their own benefits. Today, we’ll look at how each method works and why it is so useful for achieving high-quality busbars.
Powder-Coated Busbars
Powder coating is a free-flowing dry powder application that uses an electric charge to fuse the coating to the metal surface.
Powder coating is a free-flowing dry powder application that uses an electric charge to fuse the coating to the metal surface. Powder-coated busbars are electrical conductors that have been coated with a durable, non-porous layer of powder, typically applied electrostatically and cured under heat. This coating enhances their performance, durability, and safety in various applications.
Benefits of Powder-Coated Busbars
Protection and Insulation
The primary purpose of powder coating is to provide both protection and insulation. This reduces the risk of short circuits and makes busbars more durable, safeguarding them against mechanical wear and tear, moisture, and heat.
Safety
Powder-coated busbars can be safer in the long term than uncoated busbars, and those insulated with rubber and plastic are more susceptible to cracking. The durable coating enhances their resistance to scratches, cuts, and cracks, reducing the electrocution risk. Wear and tear that exposes bare metal can be dangerous, so a robust coating is essential to protect crews and staff.
Less Galvanic Corrosion
Busbars often contact other metal components, especially at connections using bolts or fasteners. Powder coating can help reduce the likelihood of galvanic corrosion when dissimilar metals (such as copper and aluminium) are in contact.
Advantages of Electroplated Busbars
Busbar plating is a surface treatment that coats busbars with a layer of metal to improve performance. As a key supplier of plated busbars for manufacturers worldwide, we have first-hand knowledge of the applications and benefits of electroplating busbars.
Enhanced Performance
The main reason for plating components is to improve performance. Over time, an uncoated busbar may lose conductivity due to oxidation or corrosion. Plating with metals such as tin or nickel preserves conductivity for longer. Tin plating, in particular, also improves solderability, making it ideal for the automotive sector. It also reduces the contact resistance of the component’s surface.
Space-Efficient
Electroplated busbars excel in applications where space is critical, as the plating layer is thin yet uniform, helping in compact assemblies.
Precise spacing in busbar design can be an essential factor for safety, reliability, and functionality.
Appearance
Electroplating offers a variety of finishes—silver, gold, nickel, tin, and more, allowing customers to choose the most suitable appearance and properties for their application. Some applications might require a bright appearance for visibility, and processes such as nickel plating and bright tin can do that.
Power Distribution
Copper and aluminium are already excellent conductors, but electroplating can further lower electrical resistance. For instance, copper and nickel plating provide efficient power distribution for high-current applications.
Durability
Electroplating extends a busbar’s lifespan by protecting it from environmental factors. Nickel and tin plating, in particular, help create busbars that stand up to wear and corrosion.
Oxidation Resistance
Tin plating helps to prevent oxidation in copper busbars over long periods, maintaining conductivity and reliability.
Prevention of Galvanic Corrosion
Electroplating is also effective in preventing galvanic corrosion, especially for aluminium busbars.
Nickel plating is one of the best solutions to ensure a high-quality busbar less prone to this issue.
Reduced Wear
Busbars are subject to considerable wear and tear over time. To enhance their durability, incorporating an appropriate metal layer can effectively shield the base material from mechanical wear, oxidation, and various environmental influences. It’s essential to take these factors into account during the design phase to select the most suitable surface treatment for the specific application environment. For instance, in situations where there are frequent sliding connections and numerous contact points, nickel plating is often recommended due to its excellent wear resistance properties.
Conclusion
Two things are undeniably vital, busbars play a key role across various industries, delivering essential benefits for efficient power distribution and more. Coating them is fundamental for longevity, resistance to corrosion, enhanced conductivity, and an improved aesthetic. Therefore, the choice between powder coating and electroplating hinges on your unique needs.