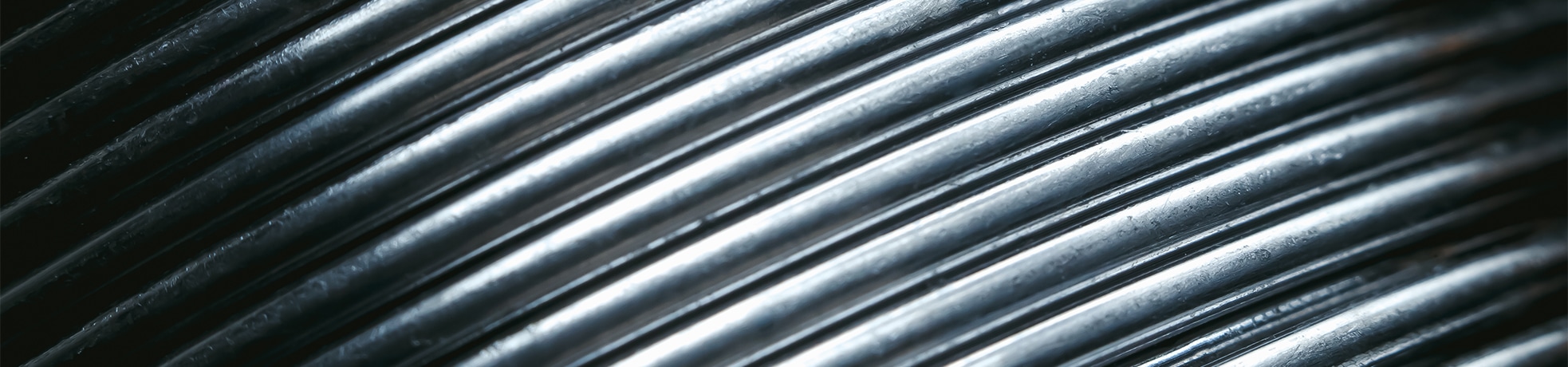
When discussing the various metals used for electroplating components, tin is rarely one of the first that comes to mind. It’s not as flashy as silver or gold, nor is it as ubiquitous as zinc or copper. However, tin is a hugely useful material, with several important benefits. In this article, we will discuss some of the benefits of tin plating, as well as the methods by which it can be applied to your substrate.
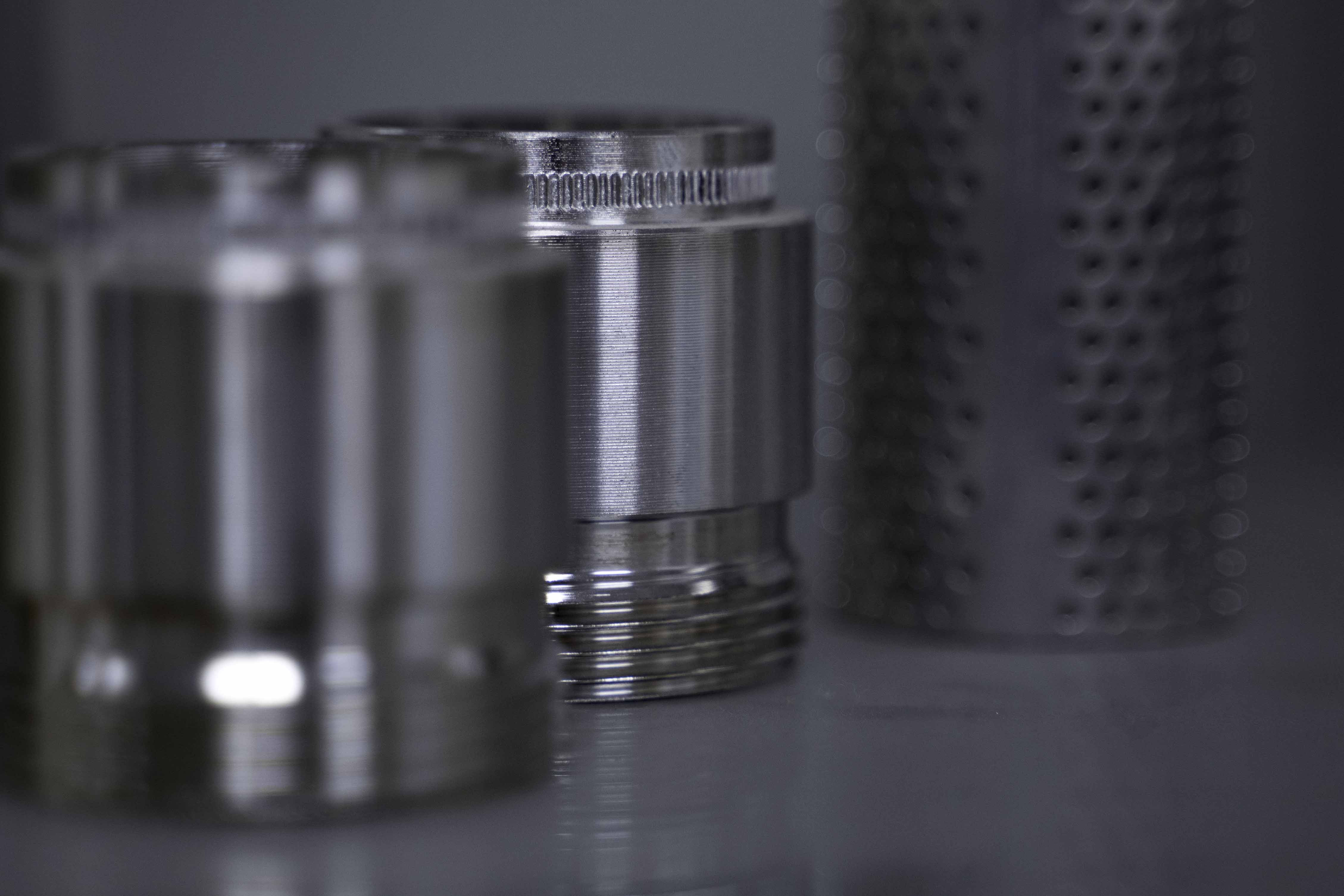
Properties of tin
Tin has several advantageous properties that make it a useful form of electro-plating. It offers good resistance against corrosion, which is always handy. It is also a highly ductile metal, meaning it can be bent, twisted, and manipulated, without weakening at the point of stress. In addition, tin is excellent for soldering and has a low transfer resistance. Both of these qualities make it popular in the electronics and electric sectors.
One property of tin that should not be overlooked is its comparative cheapness compared to other metals. Tin is extremely cost-effective, being readily available in large quantities. While it may not be as conductive, nor as corrosive-resistant as gold, silver, or platinum, in many applications the cost benefits far outweigh this.
Applications of tin plating
As already mentioned, tin-plating is a popular process in the electronics industry, where its high solderability and low cost makes it an attractive choice. Likewise, it’s used a lot in the telecommunications sector for the same reasons. Since tin is non-toxic and corrosion-resistant, it is also used extensively in the food production industry.
Bright and Dull Tin Plating
There are two types of tin plating available – bright and dull – named for their finish. Dull tin plating has a simple matte finish, while bright tin plating has a more lustrous sheen. This comes from the size of the tin grains that are deposited on the substrate during the plating process. As well as aesthetics, there are other differences between the two techniques, which we went into in detail in an earlier blog.
Drawbacks
There are two notable disadvantages to using tin – namely whiskering and perishable solderability, but both can be countered with a bit of preparation and foresight.
Whiskering is the forming of small, sharp protrusions that form on the surface of your plated tin surface. Whiskering normally occurs following the plating process, producing microscopic fibres that are invisible to the naked eye. Since tin is highly-conductive, these whiskers have been known to cause shorts in electronic devices. While there is no cure-all solution to whiskering, using dull tin plating can reduce the risk, thanks to its larger tin grains.
Perishable solderability refers to the fact that, while tin offers great solderability, this can diminish over time. Fortunately, this can be extended by proper preparation of the substrate – something that we pride ourselves on, here at Karas Plating.
Looking for more detail?
If you’re seriously considering tin plating for your components or finished products, our comprehensive guide goes further. It covers the full plating process, types of tin plating available, supply chain and sourcing considerations, and the performance benefits in greater depth.
Whether you’re a manufacturer sourcing finishes or an end user with questions about whiskering, solderability or plating compatibility, this guide is designed to help you make informed decisions.