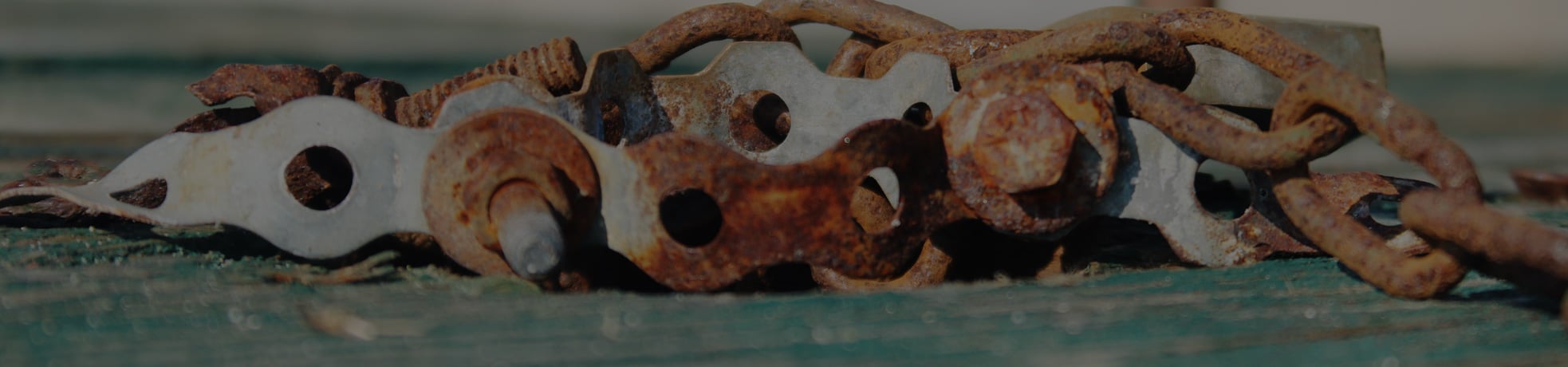
Of the various metal components that we are asked to plate or finish, some of the most common materials are iron and steel. This is hardly surprising – both metals are easy to manufacture and manipulate, while also possessing excellent strength and durability. This makes them ideal choices for a range of applications, from the smallest of fasteners to the largest construction elements.
However, both these metals (including their variations, such as cast iron, wrought iron, carbon steel, stainless steel, and engineering steel) have a shared weakness. As ferrous metals (these are metals that contain significant amounts of iron), if left unprotected they are likely to suffer damage from rust when exposed to the elements. Fortunately, there are several plating techniques that we can apply that will minimise that risk.
What is rust?
The chemical definition of rust is iron oxide (Fe²O³). It is formed by iron and oxygen reacting with one another in the presence of moisture, which acts as a catalyst. This moisture can be anything from full submersion in a body of water, through day-to-day exposure to rain, or even down to naturally occurring moisture in the air. Rust eats away at all kinds of ferrous metals gradually converting the iron present in the substrate to iron oxide.
How do I protect against rust?
The most effective way to protect your iron and steel substrate from rust is to apply a corrosion-resistant layer of metal plating. This forms an airtight seal around the substrate, preventing both moisture and oxygen from reaching the iron and causing the oxidising reaction that leads to the development of rust.
What plating methods are best for preventing rust?
While there are several metals that have corrosion-resistant qualities, some of them (such as silver and gold) are only applied in special circumstances, owing to their cost. For general use, the two most common metals are zinc and nickel.
Zinc Plating
Zinc is applied to your substrate via electrodeposition (or electroplating, as it is more commonly known). This form of finish creates a distinct layer of zinc on the surface of your base metal, which acts as a sacrificial barrier against moisture and oxygen.
While zinc alone is an effective way to prevent rust, many clients prefer a zinc-nickel alloy solution instead, as this offers longer lasting protection against corrosion.
Electroless Nickel Plating
As the name suggests, electroless nickel plating is a method of plating your iron and steel components with nickel, without using an electrical current. Rather, the metal is deposited by means of an autocatalytic chemical reaction. The process involves submerging the substrate in a solution of nickel salt and a phosphorus-based reducing agent.
Electroless nickel plating can be easily controlled to deliver the perfect results, producing a different thickness of plating for different applications and resulting in a uniform finish. Moreover, by changing the level of phosphorous in the solution, you can create a finish that works more effectively in alkaline or acidic environments.