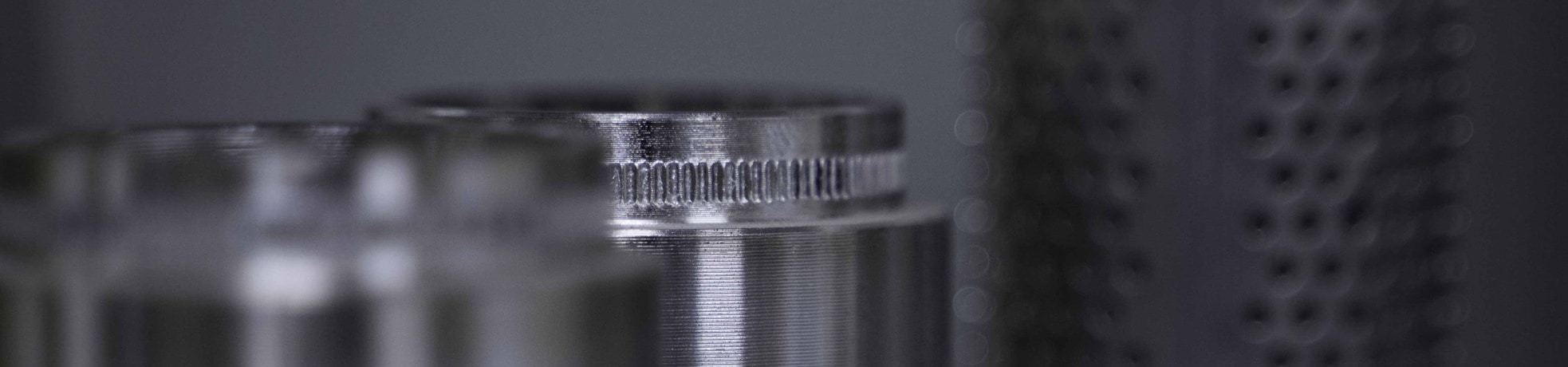
Comparing Bright Tin Plating to Dull Tin Plating
Appearance
The most noticeable difference between the two processes is an aesthetic one. As the names suggest, dull tin plating produces a matte finish with a dull, white surface. Bright tin plating, on the other hand, results in a finish that is more shiny and reflective. While bright tin plating may be more visually appealing, it is worth noting that it can become discoloured under exposure to high temperatures, tarnishing to a brown or black colour, while dull tin plating retains its original colour under similar conditions.
Composition
While both types of tin plating are essentially 100% pure tin, there are some additional organic elements in there, with the most common being carbon. Dull tin plating has less additives than its bright tin counterpart (around 0.005% to 0.05% by weight, compared to 0.1% to 1.0% by weight for bright tin). Conversely, bright tin has a smaller grain size than dull tin. This leads to a more uniform surface, which is what gives it its shiny appearance.
Solderability
If your are plating components for reflow soldering under high temperatures (between 250°C and 260°C), then dull tin plating is ideal for your needs. It is also suitable with both lead alloys and lead-free solders. As mentioned above, bright tin often discolours under higher temperatures and the material stress it incurs can lead to it becoming brittle.
Whiskering
Whiskers are small, thin fibres of metal, microscopic in size, that can grow from tin plated surfaces. More common with the bright tin plating method, owing to its small grain size, whiskering is known to create short circuits between electrical components, resulting in electrical failures.