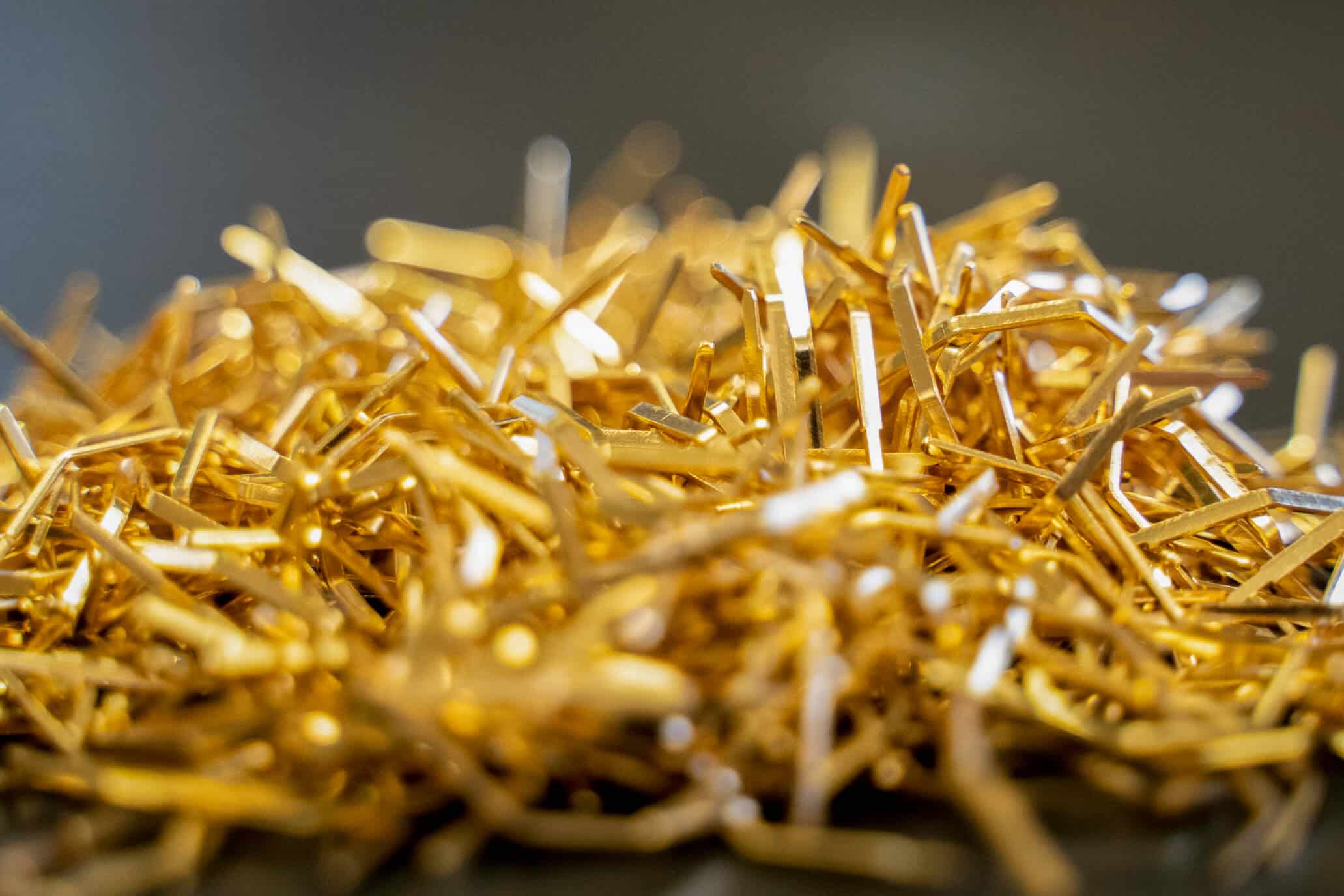
Tied to the rack or over a barrel? Your choice of plating techniques
When it comes to plating smaller components in bulk orders, there are a couple of options available. By far the most popular are barrel plating and rack plating. Here at Karas Plating, we have been using both processes for decades. They are fast and efficient methods for mass plating components and can be used in conjunction with most immersion-based electroplating techniques.
Here is a little more about what each process entails:
Barrel Plating Process
As a processes, barrel plating is well-named, since that’s exactly what the method comprises. We have large plastic barrels lined with cabling to conduct the required electrical current for the plating process. The components for any given batch of plating are loaded into the barrel which is then submerged into the plating solution. The barrel turns on a central axis, sending the components tumbling over one another coating all those difficult to reach parts.
Rack Plating Processes
Rack plating is a more labour-intensive process than barrel plating. Again, the process is named to perfection. It consists of a large rack, onto which individual components may be hung. Whereas barrel plated components are thrown in together, rack plated components are attached separately to the rack by individual hooks. These racks can also be used for larger items such as sheet metal and industrial machinery parts.
Which Process Is Best For You?
As with so many questions in the plating industry, the answer boils down to: it depends. More delicate components would certainly benefit from the rack plating process, as they are hung from individual hooks, preventing accidental damage. On the other hand, if you are plating some fairly hardy components – screws, bolts, and other fastenings for example – the barrel technique is ideal, handling large amounts of each, every time.