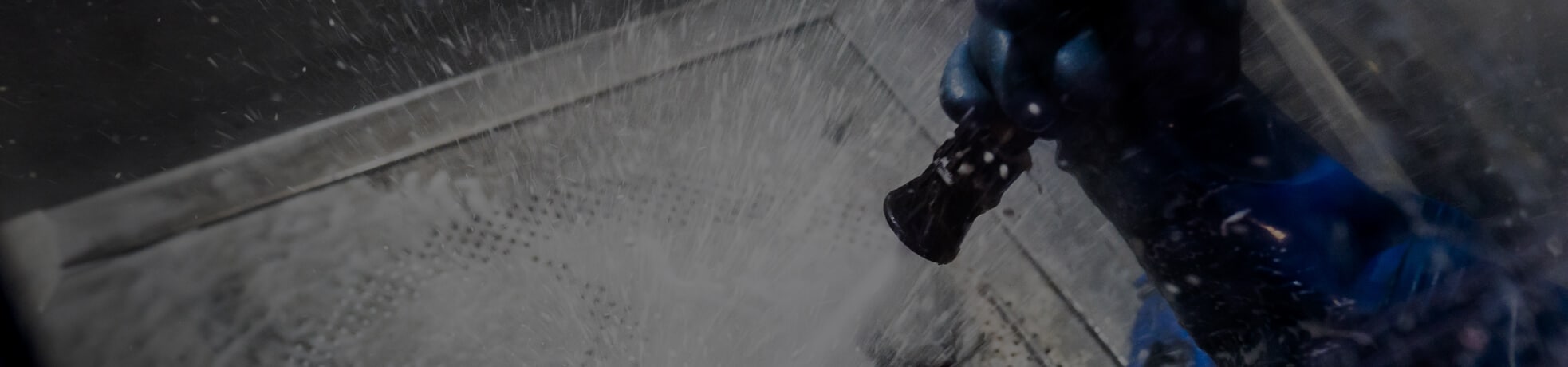
As one of the UK’s leading metal finishing and electroplating companies, much of our time is spent preparing component parts so that they accept our plating techniques. This is a crucial step in the process since, in order to perform a tight and effective bond between the metal plating (or other finish) and the substrate, the surface material must be clean of dirt, debris, grime, grease, and more.
Some of this can be done by performing a series of acid baths and rinses but sometimes – particularly with older components requiring new plating work – there is considerable caked-on dirt or corrosion that needs to be removed from the substrate. In situations like this, it needs to be abraded off, using some kind of blasting technique.
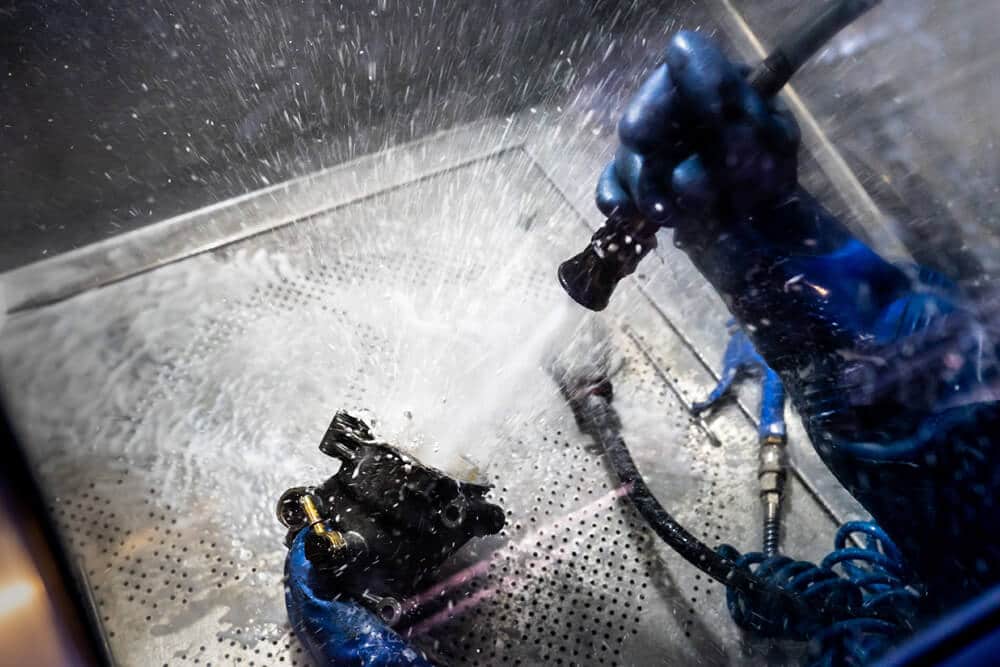
Aqua Blasting
We’ve already discussed some of the different ways components can be blasted, either for cleaning purposes, or to give them a good polish prior to plating.
In this article, we’re going to concentrate on a comparatively recent abrasion method – aqua-blasting – and some of the many benefits it offers us and our customers…
Nowhere to Hide
Unlike dry abrasive media, water can get in everywhere, tackling every nook and cranny on a given piece of substrate. All it requires is for our operators to angle the blaster in the right direction and the physics of fluid dynamics will do the rest.
Safer, More Consistent Blasting
Dry blasting equipment can damage some substrates if you’re not careful, with the high-velocity abrasive media tearing away at softer metals like aluminium. Water blasting, while equally effective at removing dirt and grime, is a more gentle cleaning method that will not damage the substrate. The spray is also more even than that from a sand blaster, giving more consistent results.
An Effective Cleaning Solution
Aqua blasting allows you to use a greater variety of abrasive media, compared to a dry-blasting format, which allows you to tailor your blasting technique more effectively. Since you can also include cleaning agents in the water, you can degrease, blast, and rinse the substrate in one go, rather than depending on separate processes to achieve the same result.
A Quieter Kind of Abrasion
Sandblasters and similar devices are noisy tools to operate and our team needs to wear suitable ear protection as the sound clocks in at anything up to 120 decibels. With slurry blasting equipment, that drops to around 75 decibels. This still needs protective headgear, but makes for a much more comfortable working environment.
Elimination of dust
Dry blasting techniques create a lot of dust as the abrasive element grinds the rust or dirt into powder, dispersing it across the blasting chamber. This requires staff to wear protective equipment over their eyes, nose, and mouth to prevent damage and irritation from the airborne dust. Under certain conditions, this dry dust can cause an explosive reaction under pressure, which is another safety concern. With aqua blasting, any dust and debris that might be abraded from the substrate is carried away with the liquid spray from our equipment – too damp to ignite and too saturated to disperse in the air.